Rapid collaborative optimization method for hybrid fiber composite material plate shell structure
A composite material board, hybrid fiber technology, applied in design optimization/simulation, special data processing applications, instruments, etc., can solve the difficult cross-scale design variable collaborative optimization of hybrid fiber composite material structures, large-scale structural optimization efficiency is low, large Problems such as low efficiency of large-scale structure calculation and optimization, to achieve the effect of reducing material cost, reducing structural quality, and meeting the needs of structural functions
- Summary
- Abstract
- Description
- Claims
- Application Information
AI Technical Summary
Problems solved by technology
Method used
Image
Examples
Embodiment Construction
[0032] In order to make the method problem solved by the present invention, the method scheme adopted and the method effect achieved clearer, the present invention will be further described in detail below in conjunction with the accompanying drawings and embodiments.
[0033] figure 1 It is an implementation flow chart of a rapid collaborative optimization method for hybrid fiber composite material plate and shell structures provided by the embodiment of the present invention. like figure 1 As shown, the embodiment of the present invention provides a fast collaborative optimization method for hybrid fiber composite plate and shell structures, including: 1) establishing an alternative material library; 2) establishing a three-dimensional finite element numerical model and performing geometric partitioning; 3) using The model reduction method is used to establish a reduced-order numerical analysis model; 4) the optimization column is established to carry out the optimization d...
PUM
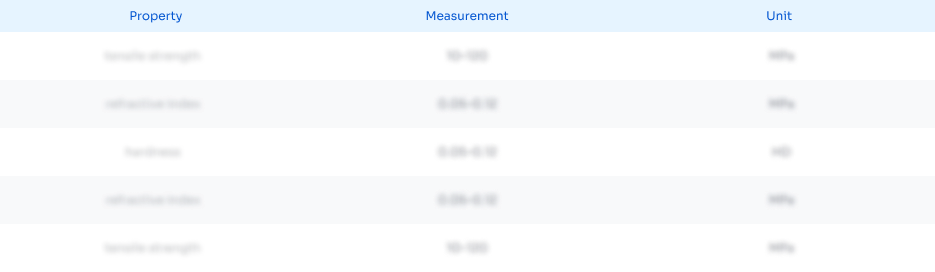
Abstract
Description
Claims
Application Information

- R&D Engineer
- R&D Manager
- IP Professional
- Industry Leading Data Capabilities
- Powerful AI technology
- Patent DNA Extraction
Browse by: Latest US Patents, China's latest patents, Technical Efficacy Thesaurus, Application Domain, Technology Topic, Popular Technical Reports.
© 2024 PatSnap. All rights reserved.Legal|Privacy policy|Modern Slavery Act Transparency Statement|Sitemap|About US| Contact US: help@patsnap.com