lidar
A laser radar and radar technology, applied in the field of ranging, can solve the problems of electromagnetic induction coil communication bandwidth that cannot meet the communication requirements of high beam laser radar, inevitable wear and tear, complex signal transmission, etc. The effect of increasing the transmission volume
- Summary
- Abstract
- Description
- Claims
- Application Information
AI Technical Summary
Problems solved by technology
Method used
Image
Examples
Embodiment 1
[0071] Embodiment 1: A laser radar, including a main shaft, a radar rotor, a base, a first main board, a second main board, an angle measurement component, a power supply component, and a communication component;
[0072] The first main board is fixedly arranged relative to the radar rotor and the first main board is arranged around the main shaft, and the second main board is fixedly arranged relative to the base and is closer to the base than the first main board ;
[0073] The angle measurement component, the power supply component and the communication component are located between the first main board and the second main board, and at least a part of the angle measurement component, at least a part of the power supply component and at least a part of the communication component surround the spindle setting;
[0074] The angle measurement component includes a first measurement module and a second measurement module, the power supply component includes a first power supply...
Embodiment 2
[0076] Embodiment 2. The lidar according to embodiment 1, wherein, in the radial direction of the main shaft, the communication component, the power supply component and the angle measurement component are arranged in sequence, and the angle measurement component is connected to the Compared with the communication component and the power supply component, the distance from the main shaft is farther.
Embodiment 3
[0077] Embodiment 3. The lidar according to Embodiment 1 or 2, wherein the first communication module includes at least one light emitting element, and the second communication module includes at least one light receiving element corresponding to the light emitting element, and
[0078] The light-emitting element moves relative to the light-receiving element, and the light-receiving element is located on the light path of at least one light beam emitted by the light-emitting element;
[0079] The light-emitting element is centered on the main axis and arranged around the main axis, forming a ring-shaped light-emitting element.
PUM
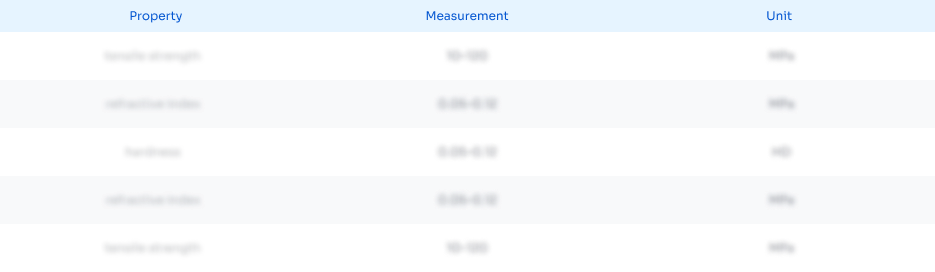
Abstract
Description
Claims
Application Information

- R&D
- Intellectual Property
- Life Sciences
- Materials
- Tech Scout
- Unparalleled Data Quality
- Higher Quality Content
- 60% Fewer Hallucinations
Browse by: Latest US Patents, China's latest patents, Technical Efficacy Thesaurus, Application Domain, Technology Topic, Popular Technical Reports.
© 2025 PatSnap. All rights reserved.Legal|Privacy policy|Modern Slavery Act Transparency Statement|Sitemap|About US| Contact US: help@patsnap.com