A Parallel Flexible Mechanism for Precision Assembly
A flexible mechanism, parallel technology, applied in the direction of manipulator, program control manipulator, comprehensive factory control, etc., can solve the problems of the compliance performance of passive compliant mechanism, the high-speed assembly of unsuitable parts under light load, and the instability of assembly inertial force assembly, etc. The effect of strong axial bearing capacity, low production cost and low cost
- Summary
- Abstract
- Description
- Claims
- Application Information
AI Technical Summary
Problems solved by technology
Method used
Image
Examples
Embodiment Construction
[0024] The present invention will be further described below in conjunction with the accompanying drawings and specific embodiments, but the following embodiments in no way limit the present invention.
[0025] like figure 1 As shown, the present invention proposes a parallel flexible mechanism for precision assembly, including an upper platform 1, a lower platform 3 and an intermediate platform 2 arranged coaxially, and a Several first flexible branch chains 4, and several second flexible branch chains are provided between the middle platform 2 and the lower platform 3. The numbers of the first flexible branch chain 4 and the second flexible branch chain 5 are both N, N≥3, figure 1 Shown is a flexible mechanism with three first flexible branches 4 and three second flexible branches 5 .
[0026] Several first flexible branch chains 4 are evenly distributed circumferentially between the upper platform 1 and the middle platform 2, and have the same size and structure; one end ...
PUM
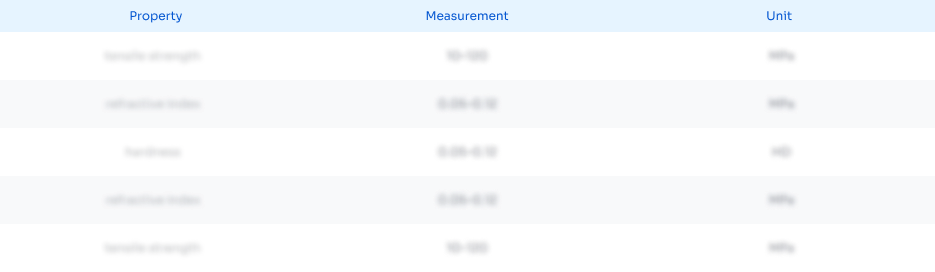
Abstract
Description
Claims
Application Information

- R&D
- Intellectual Property
- Life Sciences
- Materials
- Tech Scout
- Unparalleled Data Quality
- Higher Quality Content
- 60% Fewer Hallucinations
Browse by: Latest US Patents, China's latest patents, Technical Efficacy Thesaurus, Application Domain, Technology Topic, Popular Technical Reports.
© 2025 PatSnap. All rights reserved.Legal|Privacy policy|Modern Slavery Act Transparency Statement|Sitemap|About US| Contact US: help@patsnap.com