Numerical reconstruction method for a residual stress field of a surface strengthening metal part
A residual stress and metal component technology, applied in the fields of electrical digital data processing, special data processing applications, instruments, etc., can solve the problems of difficulty in guaranteeing validity and complicated simulation process, so as to simplify the simulation and design process, and simplify the simulation process. , Economical effect
- Summary
- Abstract
- Description
- Claims
- Application Information
AI Technical Summary
Problems solved by technology
Method used
Image
Examples
Embodiment 1
[0031] Embodiment 1: Its shape of a plate sample is as figure 1 As shown, the upper and lower surfaces of the sample have undergone surface strengthening treatment, and the mesh division in the strengthening layer area is relatively fine when dividing the mesh. Import the grid model into the finite element analysis software, set different temperature values in the strengthened layer and non-strengthened layer of the sample, and use the temperature difference to generate compressive stress in the strengthened layer area. In order to make the result more accurate, a temperature gradient can be set in different areas of the strengthening layer, such as figure 2 shown. image 3 The residual compressive stress gradient distribution for the finite element simulation. When setting the temperature, it is necessary to conduct a trial calculation based on the experimental test value to find the appropriate temperature. T high , and finally obtain the simulated residual stress fie...
Embodiment 2
[0032] Embodiment 2: The specific steps are the same as in Example 1, except that the plate-shaped sample is changed into a cylindrical sample, and the outer surface of the cylindrical sample is a surface strengthening layer. This example demonstrates that the method described in the invention is not limited by the shape of the part.
Embodiment 3
[0033] Embodiment 3: It is a T-shaped welded joint, and its weld seam strengthening area is as follows Figure 8 shown. Under the action of fatigue load, the welded structure often initiates fatigue cracks at the weld to cause component fracture and failure. Therefore, strengthening treatment will be carried out at the weld to improve its fatigue performance in engineering. Figure 9 As shown, the temperature difference can be set between the weld area and other parts of the component to simulate the residual compressive stress after the weld area is strengthened. The method shown in the invention is also applicable to more complex structures such as welded structures.
PUM
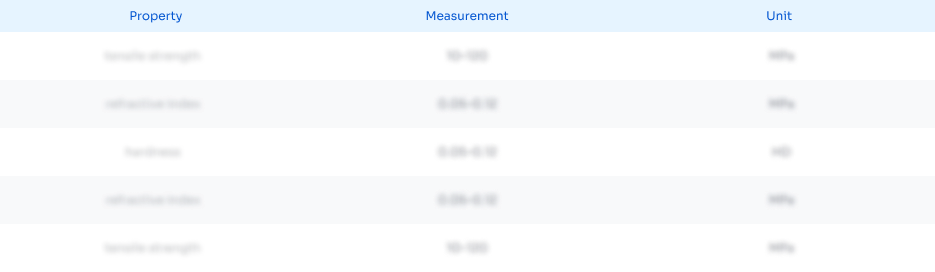
Abstract
Description
Claims
Application Information

- R&D
- Intellectual Property
- Life Sciences
- Materials
- Tech Scout
- Unparalleled Data Quality
- Higher Quality Content
- 60% Fewer Hallucinations
Browse by: Latest US Patents, China's latest patents, Technical Efficacy Thesaurus, Application Domain, Technology Topic, Popular Technical Reports.
© 2025 PatSnap. All rights reserved.Legal|Privacy policy|Modern Slavery Act Transparency Statement|Sitemap|About US| Contact US: help@patsnap.com