Double-support flange machining machine
A processing machine and double support technology, applied in the field of double support flange processing machines, can solve the problems of high difficulty of flange butt joint, flange corrosion, scratches, bumps, flange failure, etc., to reduce the difficulty of repair and Repair cost, improve repair efficiency, and ensure the effect of smooth rotation
- Summary
- Abstract
- Description
- Claims
- Application Information
AI Technical Summary
Problems solved by technology
Method used
Image
Examples
Embodiment Construction
[0015] The double-support flange processing machine has a main shaft 11, on which an inner support plate 29, a tool holder 30, and a shaft sleeve 4 are sequentially set; A plurality of screw holes 28 are evenly distributed, and screw rods 27 are housed in each screw hole, and one end of each screw rod is threadedly connected with the corresponding screw hole, and the other end of each screw rod is provided with a leg 26; The swing arm 3 is fixedly installed on the frame, the feed screw 31 and the feed motor 18 are housed on the swing arm, the feed motor is fixed on the swing arm, the motor shaft of the feed motor is connected with the leading screw power, and the feed screw Rotately connected with the swing arm, the axis line 32 of the feed screw is perpendicular to the axis line 12 of the main shaft, the feed screw nut 33 is housed on the feed screw nut, the knife seat 34 is housed on the feed screw nut, the knife seat and the rotary Arm sliding connection. The shaft sleeve ...
PUM
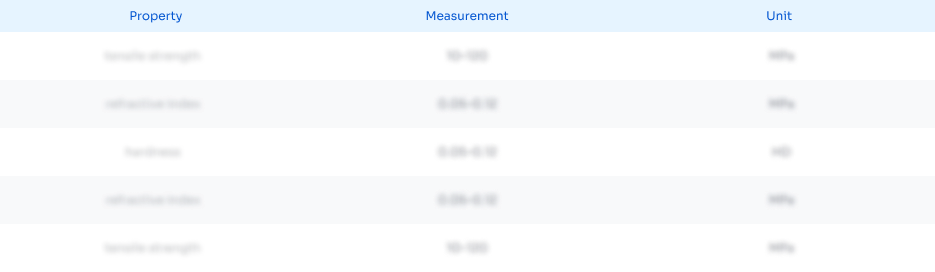
Abstract
Description
Claims
Application Information

- Generate Ideas
- Intellectual Property
- Life Sciences
- Materials
- Tech Scout
- Unparalleled Data Quality
- Higher Quality Content
- 60% Fewer Hallucinations
Browse by: Latest US Patents, China's latest patents, Technical Efficacy Thesaurus, Application Domain, Technology Topic, Popular Technical Reports.
© 2025 PatSnap. All rights reserved.Legal|Privacy policy|Modern Slavery Act Transparency Statement|Sitemap|About US| Contact US: help@patsnap.com