Nine-axis control five-axis linkage bridge type machining center and turning-milling combined machining center
A five-axis linkage and machining center technology, applied in the field of automation, can solve the problems that the machine tool cannot meet the high-precision machining requirements, does not have a Y-axis and A-axis dual-drive structure, and has poor dynamic performance, so as to improve the driving torque and dynamic response. Performance, improvement of dynamic response performance, and improvement of chip removal effect
- Summary
- Abstract
- Description
- Claims
- Application Information
AI Technical Summary
Problems solved by technology
Method used
Image
Examples
Embodiment
[0062] Mechanical structure and working principle: CNC machine tools with five-axis linkage refer to three linear feed axes and two rotary feed axes, and these five feed axes can be fed simultaneously. The three linear feed axes of CNC machine tools are The three linear feed axes of X, Y, and Z in the Cartesian coordinate system, and the two rotary feed axes can be any combination of A, B, and C axes, that is, AC combination, AB combination or BC combination.
[0063] Such as Figure 1a to Figure 1c As shown, this embodiment provides a bridge-type machining center with nine-axis control and five-axis linkage, wherein the machine tool can include: a machine tool 1, machine tool outer protection 2, control box and control unit 3, footboard 4, water cooler 5, Hydraulic station 6, electric cabinet 7, tool cooling system and chip removal system 8, pneumatic system and lubrication system 9 (installed inside the outer protection of the machine tool); special oil and air lubrication s...
Embodiment 2
[0093] On the basis of embodiment 1, this embodiment 2 provides a nine-axis control five-axis linkage bridge-type turn-milling compound machining center, the nine-axis control five-axis linkage bridge-type turn-milling compound machining center and nine-axis control five-axis linkage The difference between the bridge-type machining center is that: the direct-drive A-C cradle-type turntable is a turning-milling compound turntable to form three rotating coordinate axes; the spindle mechanism is a turning-milling electric spindle.
[0094] Other structures are the same as those in Embodiment 1, and will not be repeated here.
[0095] In summary, the nine-axis control five-axis linkage bridge-type machining center and the nine-axis control five-axis linkage bridge-type turning-milling compound machining center use nine servo-controlled axes, of which five coordinate axes can be linked, and the machine tool adopts a bridge layout , the load driven by each feed axis can be lightened...
PUM
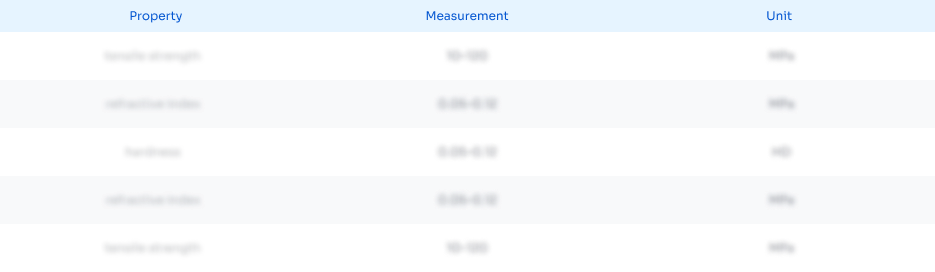
Abstract
Description
Claims
Application Information

- R&D
- Intellectual Property
- Life Sciences
- Materials
- Tech Scout
- Unparalleled Data Quality
- Higher Quality Content
- 60% Fewer Hallucinations
Browse by: Latest US Patents, China's latest patents, Technical Efficacy Thesaurus, Application Domain, Technology Topic, Popular Technical Reports.
© 2025 PatSnap. All rights reserved.Legal|Privacy policy|Modern Slavery Act Transparency Statement|Sitemap|About US| Contact US: help@patsnap.com