Resin for molding motor parts
A component and molding technology, applied in the field of resin for motor components, can solve the problems of general mechanical strength and insulation performance
- Summary
- Abstract
- Description
- Claims
- Application Information
AI Technical Summary
Problems solved by technology
Method used
Examples
Embodiment 1
[0028] The molding resin for motor parts of the present invention, in parts by weight, includes:
[0029] (1) 32 parts of ethylene glycol;
[0030] (2) 19 parts of propylene glycol;
[0031] (3) 55 parts of adipic acid;
[0032] (4) 7 parts of phthalic anhydride;
[0033] (5) 0.002 parts of dibutyltin oxide;
[0034] (6) 2 parts of dicyclopentadiene;
[0035] Its preparation method includes,
[0036] (1) Put ethylene glycol, propylene glycol, adipic acid, phthalic anhydride, dibutyltin oxide and dicyclopentadiene into the reactor in sequence, and raise the temperature to 245°C in 5 hours after feeding, and carry out the heat preservation reaction. Control and The head temperature of the condenser connected to the reactor is 96°C;
[0037] (2) After reacting for 48 hours, measure the acid value in the middle control to 48±1, then cool to 180°C, and carry out the dilution and dilution through the dilution kettle connected to the reaction kettle, in which styrene with 95% o...
Embodiment 2
[0039] The molding resin for motor parts of the present invention, in parts by weight, includes:
[0040] (1) 28 parts of ethylene glycol;
[0041] (2) 17 parts of propylene glycol;
[0042] (3) 49 parts of adipic acid;
[0043] (4) 6 parts of phthalic anhydride;
[0044] (5) 0.001 parts of dibutyltin oxide;
[0045] (6) 3 parts of dicyclopentadiene;
[0046] Its preparation method includes,
[0047] (1) Put ethylene glycol, propylene glycol, adipic acid, phthalic anhydride, dibutyltin oxide and dicyclopentadiene into the reactor in sequence, and raise the temperature to 245°C in 5 hours after feeding, and carry out the heat preservation reaction. Control and The head temperature of the condenser connected to the reactor is 96°C;
[0048] (2) React for 48 hours, measure the acid value in the middle control to 48±1, then cool to 180°C, and carry out the dilution and dilution through the dilution kettle connected to the reaction kettle, in which styrene with 90% of the tot...
PUM
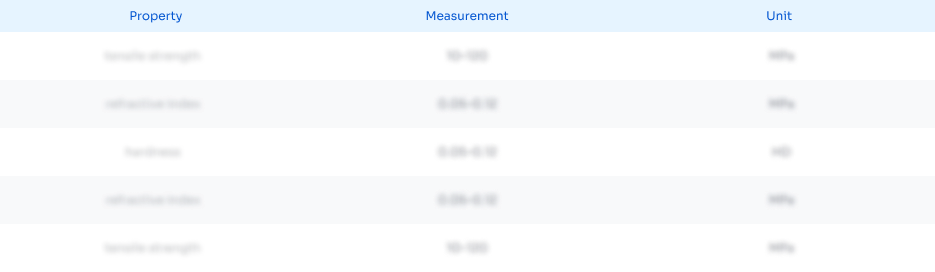
Abstract
Description
Claims
Application Information

- R&D
- Intellectual Property
- Life Sciences
- Materials
- Tech Scout
- Unparalleled Data Quality
- Higher Quality Content
- 60% Fewer Hallucinations
Browse by: Latest US Patents, China's latest patents, Technical Efficacy Thesaurus, Application Domain, Technology Topic, Popular Technical Reports.
© 2025 PatSnap. All rights reserved.Legal|Privacy policy|Modern Slavery Act Transparency Statement|Sitemap|About US| Contact US: help@patsnap.com