Main spindle device and machine tool
A kind of spindle device and spindle technology, applied in the direction of drive device, feeding device, positioning device, etc., can solve the problems of small heat generation, spindle position deviation, moving spindle and bearing, etc.
- Summary
- Abstract
- Description
- Claims
- Application Information
AI Technical Summary
Problems solved by technology
Method used
Image
Examples
no. 1 Embodiment approach ]
[0034] refer to Figure 1 to Figure 5 , the spindle device 100 of the first embodiment and the machine tool 200 including the spindle device 100 will be described.
[0035] (Outline of spindle unit and machine tool)
[0036] Such as figure 1 Shown, the main shaft device 100 is by the main shaft 10 (referring to figure 2 ) is a device for rotating and driving the tool 1 attached to one end of the main shaft 10 around the central axis to process the workpiece 3 as the workpiece. The spindle device 100 is assembled in the machine tool 200 and relatively moves with respect to the workpiece 3 by the moving mechanism 110 included in the machine tool 200 . The machine tool 200 is a numerical control (NC) machine tool, which controls the relative movement (position and speed) of the tool 1 and the workpiece 3 by means of numerical information, and executes a series of actions related to machining by means of the program 132 . Specifically, the machine tool 200 is a machining cent...
no. 2 Embodiment approach ]
[0116] Next, refer to Figure 8 and Figure 9 , the spindle device 101 of the second embodiment will be described. In the second embodiment, unlike the first embodiment in which the pressure supply to the other side axial bearing surface 21b of the axial bearing portion 21 is switched off to switch to the measurement state P2, the counter spindle 10 is set at The structure of the biasing portion 210 for biasing in the axial direction will be described. In addition, in the second embodiment, the structure other than the main shaft device 101 is the same as that of the above-mentioned first embodiment, so description thereof will be omitted. In addition, in 2nd Embodiment, the same code|symbol is attached|subjected to the same structure as said 1st Embodiment, and description is abbreviate|omitted.
[0117] Such as Figure 8 As shown, in the spindle device 101 of the second embodiment, a force applying unit 210 is provided, and the force applying unit 210 is in the measureme...
PUM
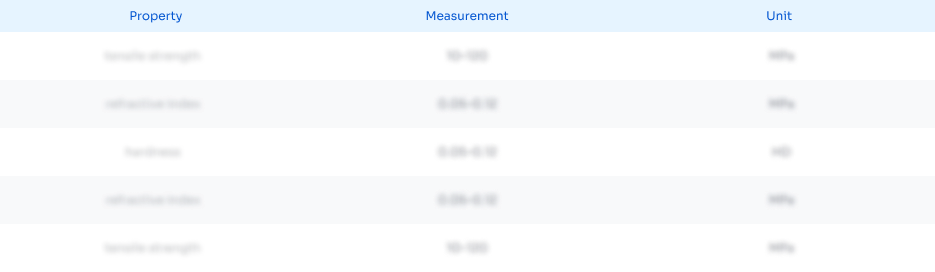
Abstract
Description
Claims
Application Information

- R&D
- Intellectual Property
- Life Sciences
- Materials
- Tech Scout
- Unparalleled Data Quality
- Higher Quality Content
- 60% Fewer Hallucinations
Browse by: Latest US Patents, China's latest patents, Technical Efficacy Thesaurus, Application Domain, Technology Topic, Popular Technical Reports.
© 2025 PatSnap. All rights reserved.Legal|Privacy policy|Modern Slavery Act Transparency Statement|Sitemap|About US| Contact US: help@patsnap.com