Curved zipper production method
A production method and zipper technology, applied in the field of zipper products, can solve the problem that the curved zipper cannot meet the traditional production process, etc., and achieve the effects of saving labor, good flexibility, and stable pulling process.
- Summary
- Abstract
- Description
- Claims
- Application Information
AI Technical Summary
Problems solved by technology
Method used
Image
Examples
Embodiment 1
[0027] refer to figure 1 , a production method of a curved slide fastener, the present embodiment is specifically a curved slide fastener with an S-shaped structure, comprising the following steps:
[0028] 1. Make a zipper tape a for carrying pairs of fastener elements, the zipper tape a is made of cotton yarn, chemical fiber or mixed chemical fiber, which contains 30% TPU material;
[0029] 2. The side edge of the opposite side of the paired zipper tape a prepared in step 1 is added with a single-strand chain element by weaving. High, low temperature and wear resistance;
[0030] 3. After step 2, carry out ironing treatment on the two zipper tapes a, the ironing temperature is between 160°C and 180°C, specifically 160°C is used here;
[0031] 4. Coating sizing agent on the front and back sides of the two zipper tapes a;
[0032] 5. Put the two zipper tapes a coated with the sizing agent into the forming mold for stretching and forming, and perform high-frequency treatment...
Embodiment 2
[0041] refer to figure 2 , compared with Embodiment 1, the curved zipper produced by this embodiment has a C-shaped structure. At this time, the number of groups of pulling sliders 1 is three groups, and the pulling sliders 1 on both sides are inclined and symmetrically arranged. , the pulling slider 1 in the middle is set perpendicular to the length direction of the two zipper tapes a. When the pulling is in progress, the running directions of the three groups of pulling sliders 1 are the same (that is, common upward or downward), so that the two zipper tapes 1 Under the action, it forms a circular arc shape bent along the running direction, which is a C-shaped structure.
PUM
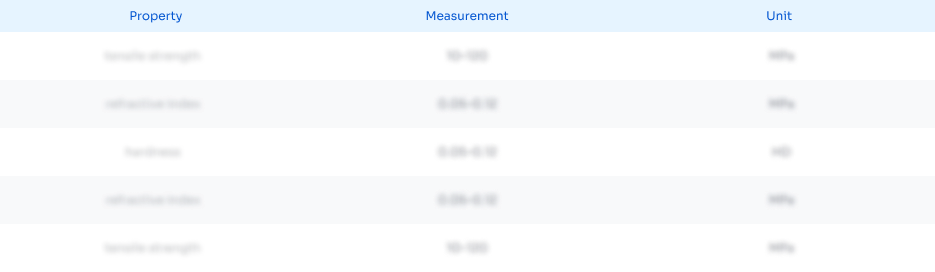
Abstract
Description
Claims
Application Information

- R&D Engineer
- R&D Manager
- IP Professional
- Industry Leading Data Capabilities
- Powerful AI technology
- Patent DNA Extraction
Browse by: Latest US Patents, China's latest patents, Technical Efficacy Thesaurus, Application Domain, Technology Topic, Popular Technical Reports.
© 2024 PatSnap. All rights reserved.Legal|Privacy policy|Modern Slavery Act Transparency Statement|Sitemap|About US| Contact US: help@patsnap.com