Cycloidal gear tooth profile linear modification method, cycloidal gear and speed reducer
A cycloidal gear tooth and cycloidal gear technology, applied in the direction of instruments, components with teeth, belts/chains/gears, etc., can solve the problems of processing, installation errors, thermal expansion and contraction, elastic deformation, etc., to ensure The effect of meshing performance
- Summary
- Abstract
- Description
- Claims
- Application Information
AI Technical Summary
Problems solved by technology
Method used
Image
Examples
Embodiment Construction
[0063] Embodiments of the present invention will be further described below in conjunction with the accompanying drawings.
[0064] The specific embodiment of cycloid gear tooth profile straight line method modification method of the present invention, as Figure 1 to Figure 7 As shown, this embodiment takes the optimal force transmission performance as the principle of calculating the modification amount, determines the modification amount of each point in the tooth profile of the cycloid, and subtracts the corresponding modification amount along the normal direction of the corresponding point , get the modified cycloid tooth profile, and carry out the simulation test to adjust the size of the modified amount.
[0065] Specifically include the following steps:
[0066] 1. Determine the distribution law of the pressure angle and the meshing phase angle of the cycloidal gear profile point
[0067] established as figure 1 The schematic diagram of the meshing state of the cycl...
PUM
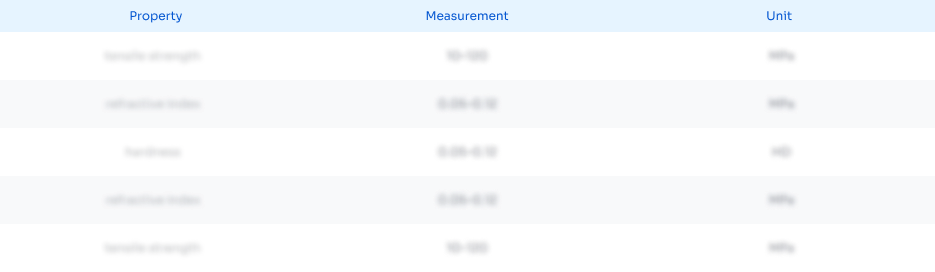
Abstract
Description
Claims
Application Information

- R&D Engineer
- R&D Manager
- IP Professional
- Industry Leading Data Capabilities
- Powerful AI technology
- Patent DNA Extraction
Browse by: Latest US Patents, China's latest patents, Technical Efficacy Thesaurus, Application Domain, Technology Topic, Popular Technical Reports.
© 2024 PatSnap. All rights reserved.Legal|Privacy policy|Modern Slavery Act Transparency Statement|Sitemap|About US| Contact US: help@patsnap.com