Spiral spring type socket
A helical wire and socket technology, applied in the direction of the base/housing, electrical components, coupling devices, etc., can solve problems such as loose connectors, socket errors, and effective contact area between pins and sockets that do not meet the design requirements. Effect of reducing impact, reducing wear degree, and smooth change of insertion force
- Summary
- Abstract
- Description
- Claims
- Application Information
AI Technical Summary
Problems solved by technology
Method used
Image
Examples
specific Embodiment approach 1
[0033] A helical wire spring socket, including an insulating outer casing 2, an inner casing 3 and several wire springs 4, the inner casing 3 is a cylindrical structure that penetrates up and down, and the side wall of the inner casing 3 is from top to bottom Several groups of through holes are provided, each group includes two layers of staggered through holes, and each layer of through holes is evenly distributed on the same horizontal plane, and each wire spring 4 passes through the same group of through holes sequentially along the circumferential direction of the inner sleeve 3 And connect end to end to form a wire spring wire ring, the inner sleeve 3 equipped with wire spring wire ring is placed inside the insulating jacket 2, the inner sleeve 3 is fixedly connected with the insulating jacket 2, the inner sleeve 3 and several wire springs 4 are conductive materials.
[0034] Further, the radius of the area surrounded by the spring wire ring inside the inner sleeve 3 incr...
Embodiment 1
[0043] A helical wire spring socket, including an insulating outer casing 2, an inner casing 3 and several wire springs 4, the inner casing 3 is a cylindrical structure that penetrates up and down, and the side wall of the inner casing 3 is from top to bottom Several groups of through holes are provided, each group includes two layers of staggered through holes, the number of each layer of through holes is three, and each layer of through holes is evenly distributed on the same horizontal plane. The circumferential direction passes through the same group of through holes in turn and connects end to end to form a wire spring wire ring. The inner sleeve 3 equipped with the wire spring wire ring is placed inside the insulating jacket 2, and the inner sleeve 3 is fixedly connected with the insulating jacket 2. The inner sleeve 3 and several wire springs 4 are all conductive materials.
[0044] Further, the radius of the area surrounded by the wire spring wire ring increases sequen...
Embodiment 2
[0050] A helical wire spring socket, including an insulating outer casing 2, an inner casing 3 and several wire springs 4, the inner casing 3 is a cylindrical structure that penetrates up and down, and the side wall of the inner casing 3 is from top to bottom Several groups of through holes are provided, and each group includes two layers of staggered through holes. The number of through holes in each layer is five, and the through holes in each layer are evenly distributed on the same horizontal plane. The circumferential direction passes through the same group of through holes in turn and connects end to end to form a wire spring wire ring. The inner sleeve 3 equipped with the wire spring wire ring is placed inside the insulating jacket 2, and the inner sleeve 3 is fixedly connected with the insulating jacket 2. The inner sleeve 3 and several wire springs 4 are all conductive materials.
[0051] Further, the radius of the area surrounded by the wire spring wire ring increase...
PUM
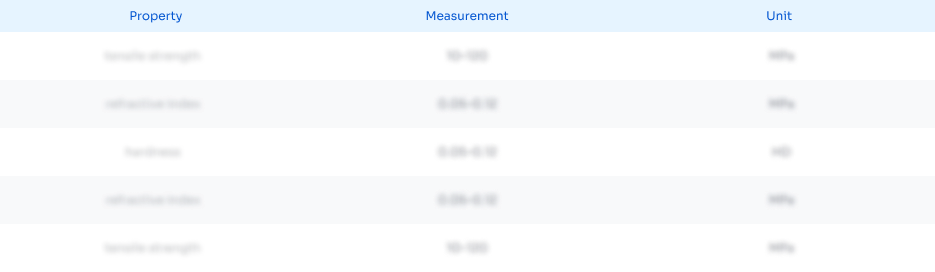
Abstract
Description
Claims
Application Information

- R&D Engineer
- R&D Manager
- IP Professional
- Industry Leading Data Capabilities
- Powerful AI technology
- Patent DNA Extraction
Browse by: Latest US Patents, China's latest patents, Technical Efficacy Thesaurus, Application Domain, Technology Topic, Popular Technical Reports.
© 2024 PatSnap. All rights reserved.Legal|Privacy policy|Modern Slavery Act Transparency Statement|Sitemap|About US| Contact US: help@patsnap.com