A spatial complex multi-branch pipe column joint bearing capacity calculation method
A computing method, a technology of manifolds, applied in computing, instrumentation, electrical digital data processing, etc.
- Summary
- Abstract
- Description
- Claims
- Application Information
AI Technical Summary
Problems solved by technology
Method used
Image
Examples
Embodiment
[0023] A method for calculating the bearing capacity of space-complex multi-branch joints, comprising the following steps:
[0024] S1. Establish the finite element model of the complex multi-branch pipe string in space; use the software ANSYS to model, establish such as figure 1 The finite element model shown includes the main pipe 1, the fourth branch 2, the first branch 3, the fifth branch 4, the second branch 5, the third branch 6 and the first auxiliary material rod 7, and the node model is simulated by SHELL181 shell element , regardless of the influence of the weld, the connection between the member and the gusset plate bolt hole is simulated by the MPC184 unit.
[0025] Considering the geometric nonlinearity and material nonlinearity of the joint model, the constitutive relationship of steel adopts multi-linear model and isotropic strengthening theory.
[0026] S2. Splitting the finite element model of the spatially complex multi-branch pipe string to obtain the K-typ...
PUM
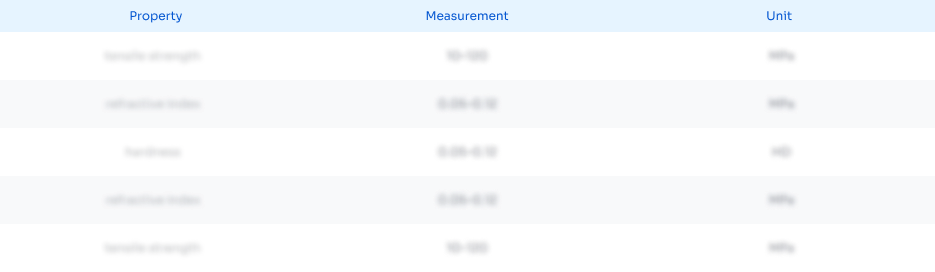
Abstract
Description
Claims
Application Information

- R&D Engineer
- R&D Manager
- IP Professional
- Industry Leading Data Capabilities
- Powerful AI technology
- Patent DNA Extraction
Browse by: Latest US Patents, China's latest patents, Technical Efficacy Thesaurus, Application Domain, Technology Topic, Popular Technical Reports.
© 2024 PatSnap. All rights reserved.Legal|Privacy policy|Modern Slavery Act Transparency Statement|Sitemap|About US| Contact US: help@patsnap.com