Medicinal PVC (Polyvinyl Chloride) hard sheet and production process thereof
A hard sheet and antistatic agent technology, applied in the field of pharmaceutical PVC hard sheet and its production process, can solve problems such as high surface resistance, drug pollution, and quality decline of PVC hard sheet, so as to enhance antistatic performance and increase antibacterial rate , to avoid the effect of bacterial contamination of drugs
- Summary
- Abstract
- Description
- Claims
- Application Information
AI Technical Summary
Problems solved by technology
Method used
Image
Examples
Embodiment 1
[0048] A pharmaceutical PVC hard sheet, comprising the following parts by weight:
[0049] 80 parts of PVC;
[0050] 10 copies of EVOH, model L171B, purchased from Kuraray, Japan;
[0051] 5 copies of PE-g-MAH, model TY 1052H, purchased from Dow in the United States;
[0052] Acetyl tri-n-butyl citrate 3 parts;
[0053] 2 parts of stabilizing agent, and stabilizing agent comprises cerium stearate, zinc stearate and pentaerythritol that mass ratio is 2:2:1;
[0054] 6 parts of antistatic agent;
[0055] 0.4 parts of lubricant;
[0056] Antibacterial powder 4 parts.
[0057] The preparation process of the antistatic agent is as follows; in parts by weight, first mix 4 parts of dodecylamine, 16 parts of epichlorohydrin, and 160 parts of methanol and continue to stir for 4 hours, then add 18 parts of TMHDA, heat up to 55 ° C, and react for 10 hours , dialyzed to obtain a reaction solution, and finally vacuum-dried to obtain an antistatic agent.
[0058] The preparation proces...
Embodiment 2
[0069] A pharmaceutical PVC hard sheet, comprising the following parts by weight:
[0070] PVC 85 parts;
[0071] 15 copies of EVOH, model L171B, purchased from Kuraray, Japan;
[0072] 7 copies of PE-g-MAH, model TY 1052H, purchased from Dow in the United States;
[0073] Acetyl tri-n-butyl citrate 5 parts;
[0074] 4 parts of stabilizing agent, and stabilizing agent comprises cerium stearate, zinc stearate and pentaerythritol that mass ratio is 2:2:1;
[0075] 8 parts of antistatic agent;
[0076] 0.8 parts of lubricant;
[0077] Antibacterial powder 6 parts.
[0078] The preparation process of the antistatic agent is as follows; in parts by weight, first mix 7 parts of dodecylamine, 20 parts of epichlorohydrin, and 180 parts of methanol and continue to stir for 5 hours, then add 20 parts of TMHDA, heat up to 60 ° C, and react for 12 hours , dialyzed to obtain a reaction solution, and finally vacuum-dried to obtain an antistatic agent.
[0079] The preparation process...
Embodiment 3
[0090] A pharmaceutical PVC hard sheet, comprising the following parts by weight:
[0091] PVC 82 parts;
[0092] 12 copies of EVOH, model L171B, purchased from Kuraray, Japan;
[0093] 6 copies of PE-g-MAH, model TY 1052H, purchased from Dow in the United States;
[0094] Acetyl tri-n-butyl citrate 4 parts;
[0095] 3 parts of stabilizing agent, and stabilizing agent comprises cerium stearate, zinc stearate and pentaerythritol that mass ratio is 2:2:1;
[0096] 7 parts of antistatic agent;
[0097] Lubricant 0.6 parts;
[0098] Antibacterial powder 5 parts.
[0099] The preparation process of the antistatic agent is as follows; in parts by weight, first mix 6 parts of dodecylamine, 18 parts of epichlorohydrin, and 170 parts of methanol and continue to stir for 4.5 hours, then add 19 parts of TMHDA, heat up to 58 ° C, and react After 11 hours, dialyze to obtain the reaction solution, and finally vacuum-dry to obtain the antistatic agent.
[0100] The preparation process...
PUM
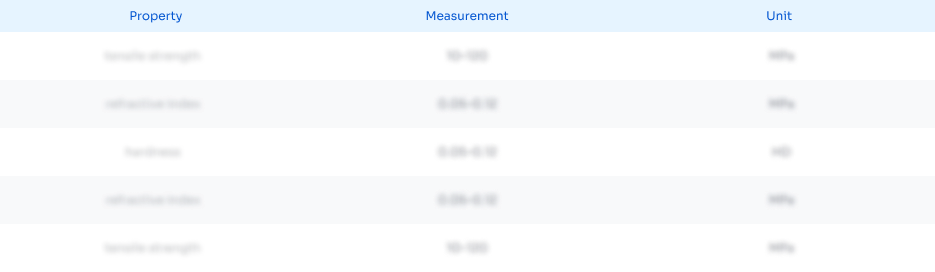
Abstract
Description
Claims
Application Information

- R&D
- Intellectual Property
- Life Sciences
- Materials
- Tech Scout
- Unparalleled Data Quality
- Higher Quality Content
- 60% Fewer Hallucinations
Browse by: Latest US Patents, China's latest patents, Technical Efficacy Thesaurus, Application Domain, Technology Topic, Popular Technical Reports.
© 2025 PatSnap. All rights reserved.Legal|Privacy policy|Modern Slavery Act Transparency Statement|Sitemap|About US| Contact US: help@patsnap.com