Vacuum smelting process for high-manganese high-aluminum high-titanium steel
A vacuum smelting, high-aluminum technology, applied in the field of metallurgy, can solve the problems of aluminum and titanium oxidation loss, manganese volatilization and oxidation loss, and achieve the effect of ensuring volatility
- Summary
- Abstract
- Description
- Claims
- Application Information
AI Technical Summary
Problems solved by technology
Method used
Examples
Embodiment 1
[0020] The target composition requirements of high manganese, high aluminum and high titanium steel are: C 0.18% (wt.), Mn 6% (wt.), Ti 8% (wt.), Al 4.5% (wt.), B 4% (wt.) .), the balance is Fe and unavoidable impurity elements.
[0021] (1) Initial melting stage: The entire initial melting stage is carried out under vacuum conditions, the pressure in the furnace is ≤30Pa, the initial charge is 48% of the total industrial pure iron and carbon particles, and the melting speed is 0.5-1kg / min. After the initial charge is completely melted and lasted for 5 minutes, Al particles are added. After the Al particles are completely melted, the content is 0.2% (wt.). The Al melting process maintains a high power of 130kW within 3 minutes to the end of full melting.
[0022] (2) Refining stage: After the initial melting, the remaining carbon particles are added to enter the refining stage. The refining temperature is 1280-1300°C, the refining time is 14 min, and the refining vacuum is 50-60 Pa...
Embodiment 2
[0028] The target composition requirements of high manganese, high aluminum, high titanium and high boron steel are: C 0.12% (wt.), Mn 6.5% (wt.), Ti 8.5% (wt.), Al 5% (wt.), B 4 % (Wt.), the balance is Fe and unavoidable impurity elements.
[0029] (1) Initial melting stage: The entire initial melting stage is carried out under vacuum conditions, the pressure in the furnace is ≤30Pa, the initial charge is 51% of the total industrial pure iron and carbon particles, and the melting speed is 0.5-1kg / min. After the initial charge is completely melted and lasted for 5 minutes, Al particles are added. After the Al particles are completely melted, the content is 0.2% (wt.). The Al melting process maintains a high power of 130kW within 3 minutes to the end of full melting.
[0030] (2) Refining stage: After the initial melting, add the remaining carbon particles to enter the refining stage, the refining temperature is 1260-1880°C, the refining time is 14min, and the refining vacuum is 50-...
PUM
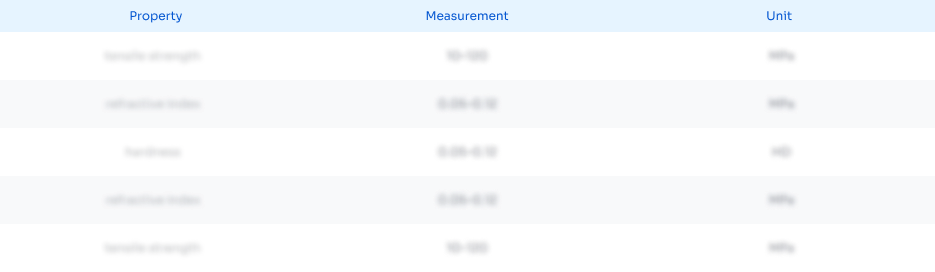
Abstract
Description
Claims
Application Information

- R&D Engineer
- R&D Manager
- IP Professional
- Industry Leading Data Capabilities
- Powerful AI technology
- Patent DNA Extraction
Browse by: Latest US Patents, China's latest patents, Technical Efficacy Thesaurus, Application Domain, Technology Topic, Popular Technical Reports.
© 2024 PatSnap. All rights reserved.Legal|Privacy policy|Modern Slavery Act Transparency Statement|Sitemap|About US| Contact US: help@patsnap.com