Vibration reduction mechanism of stator winding machine
A vibration damping mechanism and stator winding technology, applied in electromechanical devices, manufacturing motor generators, electrical components, etc., can solve the problems of speeding up parts, damage, impact winding machines, etc., and achieve the effect of reducing vibration
- Summary
- Abstract
- Description
- Claims
- Application Information
AI Technical Summary
Problems solved by technology
Method used
Image
Examples
Embodiment Construction
[0041] The technical solutions of the present invention will be further described below in conjunction with the accompanying drawings in the embodiments of the present invention.
[0042] A vibration damping mechanism of a stator winding machine, comprising a frame 10 and a winding drive mechanism,
[0043] Described winding drive mechanism comprises power source, upper fly fork lever 1, cam 2, slide block 7, winding head 5 and guide rod 8, and described guide rod 8 is vertically arranged on the frame 10, and described slide block 7 Set on the guide rod 8, the cam 2 is rotatably connected to the frame 10 and driven by a power source to rotate, the cam 2 is connected to the slider 7 through cam transmission, and the slider 7 is driven up and down along the guide rod 8 during the rotation of the cam 2 Sliding, the upper flying fork lever 1 is provided with a winding head 5, the lower end is connected with the slider 7, and the middle part is slidably connected with the frame 10,...
PUM
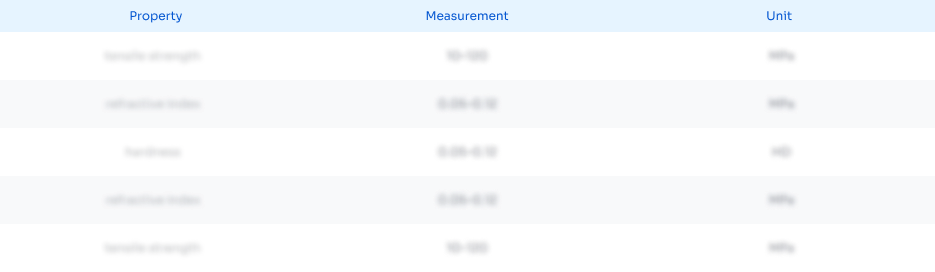
Abstract
Description
Claims
Application Information

- R&D
- Intellectual Property
- Life Sciences
- Materials
- Tech Scout
- Unparalleled Data Quality
- Higher Quality Content
- 60% Fewer Hallucinations
Browse by: Latest US Patents, China's latest patents, Technical Efficacy Thesaurus, Application Domain, Technology Topic, Popular Technical Reports.
© 2025 PatSnap. All rights reserved.Legal|Privacy policy|Modern Slavery Act Transparency Statement|Sitemap|About US| Contact US: help@patsnap.com