A kind of manufacturing method of powder material high temperature calcining rotary furnace furnace tube
The technology of a powder material and production method is applied in the field of production of powder material high-temperature calcined rotary furnace tubes, which can solve the problems of large nitrogen gas consumption, large power consumption, and low production efficiency, and achieve fast heat conduction, Nitrogen consumption savings and high production efficiency
- Summary
- Abstract
- Description
- Claims
- Application Information
AI Technical Summary
Problems solved by technology
Method used
Image
Examples
Embodiment Construction
[0019] The following will clearly and completely describe the technical solutions in the embodiments of the present invention with reference to the accompanying drawings in the embodiments of the present invention. Obviously, the described embodiments are only some, not all, embodiments of the present invention. Based on the embodiments of the present invention, all other embodiments obtained by persons of ordinary skill in the art without making creative efforts belong to the protection scope of the present invention.
[0020] see Figure 1-7 , the present invention provides a technical solution: a method for manufacturing a powder material high-temperature calcined rotary furnace tube, the furnace tube is welded together by a tube body (1), a spiral piece (2), and a connecting rod (3), The pipe body (1) is provided with three sections of connecting rod (3) installation holes evenly distributed for welding and fixing the positioning of the helical piece (2), and the helical p...
PUM
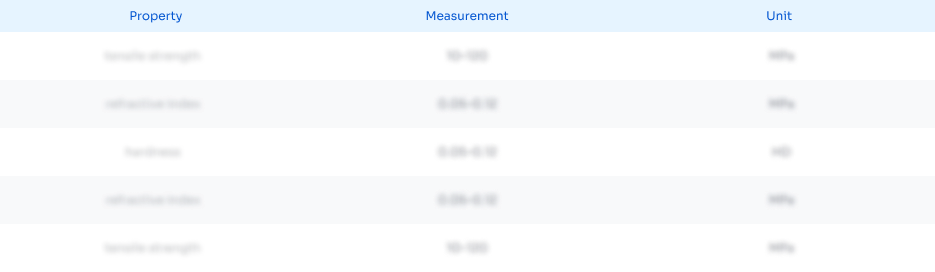
Abstract
Description
Claims
Application Information

- R&D
- Intellectual Property
- Life Sciences
- Materials
- Tech Scout
- Unparalleled Data Quality
- Higher Quality Content
- 60% Fewer Hallucinations
Browse by: Latest US Patents, China's latest patents, Technical Efficacy Thesaurus, Application Domain, Technology Topic, Popular Technical Reports.
© 2025 PatSnap. All rights reserved.Legal|Privacy policy|Modern Slavery Act Transparency Statement|Sitemap|About US| Contact US: help@patsnap.com