Rolling bearing structure into which wheel speed sensor is embedded
A wheel speed sensor, rolling bearing technology, applied in bearing components, shafts and bearings, bearing assembly and other directions, can solve the problems of poor signal-to-noise ratio, difficult rolling bearing slip rate, high price of vibration sensors and their matching acquisition devices, etc. Ease of use and low cost
- Summary
- Abstract
- Description
- Claims
- Application Information
AI Technical Summary
Problems solved by technology
Method used
Image
Examples
Embodiment 1
[0023] Example 1, such as Figure 1-Figure 3 As shown, a rolling bearing structure with a built-in wheel speed sensor, including a rolling bearing composed of an outer ring 1, a roller 2, a cage 3 and an inner ring 4, and a sensor body 5 and a cage 3 fixed on the inner hole of the outer ring 1 The ring gear on the top constitutes a magnetoelectric wheel speed sensor, and the non-contact measurement method does not affect the normal operation of the rolling bearing; the ring gear of the magnetoelectric wheel speed sensor and the cage 3 are integrated, and the tooth height of the ring gear is based on the wheel The working range of the speed sensor probe is designed so that the distance between the installed sensor body 5 and the ring gear is within the normal working range of the magnetoelectric wheel speed sensor. When the outer ring 1, roller 2, cage 3, inner ring When a partial fault occurs in components such as 4, the instantaneous speed signal of the cage 3 collected by th...
Embodiment 2
[0025] In Embodiment 2, the fixed form and position of the sensor body 5 are not limited to the form shown in Embodiment 1. Since the sensor body 5 is mainly used to measure the instantaneous rotational speed of the cage 3, as long as it can be fixed on a non-rotating part, The sensor probe can be aligned with the ring gear on the cage 3, for example, the sensor body 5 is fixed on the outer ring 1 in the form of a bracket 6, such as Figure 4-Figure 6 structure shown.
[0026] The tooth direction of the ring gear on the cage 3 can be made radial, such as Figure 1-Figure 3 As shown, it can also be made axial, such as Figure 4-Figure 6 shown.
[0027] The working principle of the magnetoelectric wheel speed sensor: when the shaft connected to the inner ring 4 rotates, the cage 3 rotates at its characteristic frequency, and the ring gear on one side continuously cuts the magnetic force lines of the permanent magnet core 5-3 to generate electrical signals , the fault diagnosi...
PUM
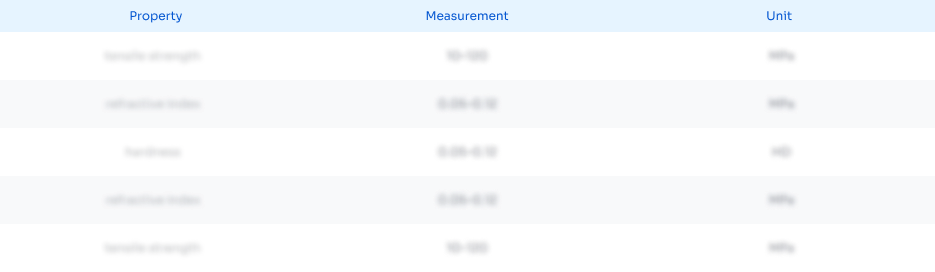
Abstract
Description
Claims
Application Information

- R&D Engineer
- R&D Manager
- IP Professional
- Industry Leading Data Capabilities
- Powerful AI technology
- Patent DNA Extraction
Browse by: Latest US Patents, China's latest patents, Technical Efficacy Thesaurus, Application Domain, Technology Topic, Popular Technical Reports.
© 2024 PatSnap. All rights reserved.Legal|Privacy policy|Modern Slavery Act Transparency Statement|Sitemap|About US| Contact US: help@patsnap.com