Early fault identification method of rolling bearing under variable rotating speed working condition
A technology of rolling bearings and recognition methods, applied to the recognition of patterns in signals, character and pattern recognition, testing of mechanical components, etc.
- Summary
- Abstract
- Description
- Claims
- Application Information
AI Technical Summary
Problems solved by technology
Method used
Image
Examples
Embodiment
[0082] In this embodiment, the method designed in the present invention will be verified by using a set of simulation signals of rolling bearing outer ring faults under increasing speed conditions. The duration of the simulated signal is 10s, and the sampling frequency is fs=12800Hz. Under the condition of rotation frequency 1Hz, the fault characteristic frequency of bearing outer ring is 5.4Hz. The impact signal of a bearing with a single fault cycle under the condition of increasing speed is expressed as:
[0083]
[0084] a i =(T i / 10) 2 i=1,2,...,n (7)
[0085] In formula (6) and formula (7): t i is the duration of a single fault cycle; t i =a i is the shock amplitude fluctuation coefficient caused by the speed-up condition, T i is the moment corresponding to the i-th impact, and n is the number of fault cycles contained within 10s.
[0086] Combining the generated n single fault shocks can obtain the bearing outer ring fault shock signal B(t) in the whole ti...
PUM
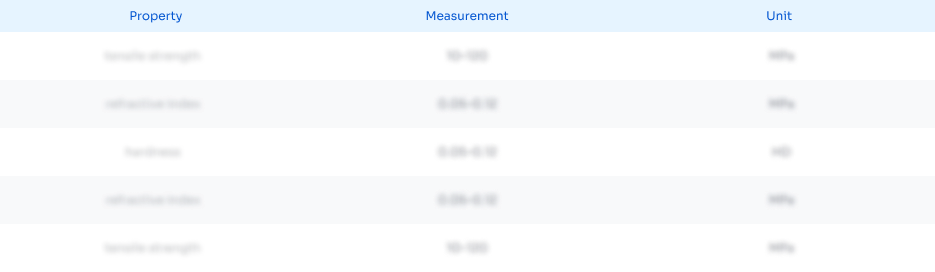
Abstract
Description
Claims
Application Information

- R&D
- Intellectual Property
- Life Sciences
- Materials
- Tech Scout
- Unparalleled Data Quality
- Higher Quality Content
- 60% Fewer Hallucinations
Browse by: Latest US Patents, China's latest patents, Technical Efficacy Thesaurus, Application Domain, Technology Topic, Popular Technical Reports.
© 2025 PatSnap. All rights reserved.Legal|Privacy policy|Modern Slavery Act Transparency Statement|Sitemap|About US| Contact US: help@patsnap.com