Single rotor wing unmanned aerial vehicle
A drone and single-rotor technology, applied in the field of drones, can solve problems such as output shaft vibration, imprecise meshing of the driven gear plate, deflection and rotation set value errors, etc., to avoid axial creep and prevent The effect of turning the belt over to ensure stability
- Summary
- Abstract
- Description
- Claims
- Application Information
AI Technical Summary
Problems solved by technology
Method used
Image
Examples
Embodiment
[0074] Embodiment: a kind of single-rotor UAV, such as figure 1 Shown: including UAV body and flight power system, the UAV body includes main body 601, tail pipe 602 and wake box 702, one end of the tail pipe is connected to the main body and the other end is connected to Wake box, the flight power system includes a rotor mechanism and a drive system, the rotor mechanism is connected to the drive system, the rotation and deflection of the rotor mechanism are driven by the drive system, and the rotor mechanism includes a main rotor mechanism 30 and an empennage mechanism 70, the main rotor mechanism is located at the main fuselage, and the empennage mechanism is located at the wake box;
[0075] Such as figure 2 As shown: the main body includes a power bin 6011 and a power bin 6012 for placing batteries, the power bin is located above the power bin, and the power bin is connected to the power bin through studs 603, the A fuselage reinforcement plate 604 is provided between t...
PUM
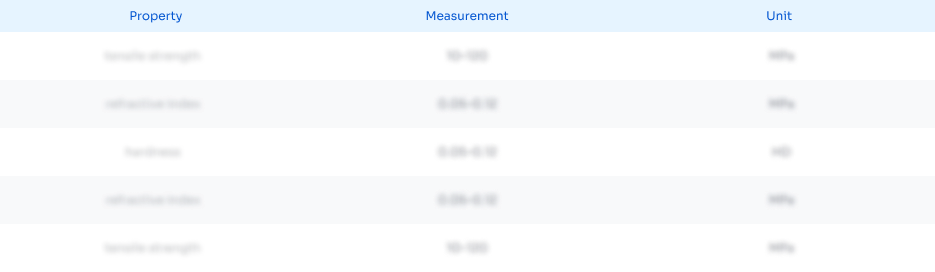
Abstract
Description
Claims
Application Information

- R&D
- Intellectual Property
- Life Sciences
- Materials
- Tech Scout
- Unparalleled Data Quality
- Higher Quality Content
- 60% Fewer Hallucinations
Browse by: Latest US Patents, China's latest patents, Technical Efficacy Thesaurus, Application Domain, Technology Topic, Popular Technical Reports.
© 2025 PatSnap. All rights reserved.Legal|Privacy policy|Modern Slavery Act Transparency Statement|Sitemap|About US| Contact US: help@patsnap.com