Main rotary wing system of single rotary wing UAV (Unmanned Aerial Vehicle)
A main rotor and UAV technology, applied in the field of UAV, can solve the problems of deflection and rotation set value error, deflection can not reach the predetermined angle, thrust bearing axial clearance is large, etc., to improve accuracy and rigidity Big, smooth flipping effects
- Summary
- Abstract
- Description
- Claims
- Application Information
AI Technical Summary
Problems solved by technology
Method used
Image
Examples
Embodiment
[0050] Embodiment: the main rotor system of a kind of single-rotor unmanned aerial vehicle, as figure 1 Shown: comprising a main rotor mechanism 30 and a drive system 40 for driving said main rotor mechanism;
[0051] The main rotor mechanism includes a main rotor head 302 fixedly connected to the main shaft 401 of the drone, and the main rotor head is vertically arranged with the main shaft;
[0052] like figure 2 , image 3 and Figure 4 As shown: the main rotor head includes a central paddle seat 3021, the central paddle seat has a vertical arm 30211 and a cross arm 30212, and the central paddle seat is formed into a "T" shape by the cross arm and the vertical arm structure, the vertical arm is fixedly connected to the main shaft, and both ends of the cross arm are provided with a main blade clamp 3022 for clamping the main rotor, and one end of the main blade clamp is sleeved on the cross arm, and the Thrust bearing 3023 and at least one angular contact bearing 3024 a...
PUM
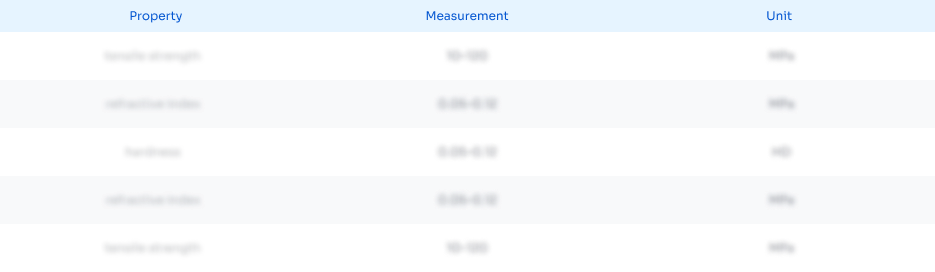
Abstract
Description
Claims
Application Information

- R&D
- Intellectual Property
- Life Sciences
- Materials
- Tech Scout
- Unparalleled Data Quality
- Higher Quality Content
- 60% Fewer Hallucinations
Browse by: Latest US Patents, China's latest patents, Technical Efficacy Thesaurus, Application Domain, Technology Topic, Popular Technical Reports.
© 2025 PatSnap. All rights reserved.Legal|Privacy policy|Modern Slavery Act Transparency Statement|Sitemap|About US| Contact US: help@patsnap.com