Magnetic adsorption type wall-climbing robot system
A wall-climbing robot and magnetic adsorption technology, applied in motor vehicles, auxiliary devices, auxiliary welding equipment, etc., can solve the problems of unguaranteed welding accuracy, difficult disassembly and unloading, affecting product quality, etc., to increase flexibility and Load capacity, improved carrying capacity, weight reduction effect
- Summary
- Abstract
- Description
- Claims
- Application Information
AI Technical Summary
Problems solved by technology
Method used
Image
Examples
Embodiment 1
[0029] The following is attached Figure 1-6 Embodiments of the invention are described in detail, but the invention can be practiced in many different ways as defined and covered by the claims.
[0030] The present invention provides a magnetic adsorption wall-climbing robot comprising a car body 2, a magnetically conductive wheel 1 and a magnetic control device 3, the magnetically conductive wheel 3 is arranged under the car body 2, and the magnetic control device 3 is arranged on the In the magnetic permeable wheel 1, it is used to control the change of the magnetic field intensity around the magnetic permeable wheel 1. The adsorption and unloading of the magnetic permeable wheel 1 can be effectively realized, and the robot can be easily disassembled and unloaded. The car body 2 is made of an aluminum alloy material, and the car body 2 includes a mounting plate 21 and two cavities 22, and the cavities 22 are welded on the left and right sides of the lower surface of the mo...
Embodiment 2
[0040] Changing the four-wheel four-wheel drive robot described in Embodiment 1 into a three-wheel three-wheel drive structure can further reduce the weight of the robot, improve flexibility, and increase load capacity.
[0041] The invention provides a magnetic adsorption wall climbing machine. The robot includes a car body 2 and a magnetically conductive wheel 1. A magnetic force control device 3 is arranged under the car body 2. The car body 2 includes a mounting plate 21 and two cavities. Body 22, the cavity 22 is welded on the left and right sides of the lower surface of the mounting plate 21, the cavity 22 is used to protect the exposed equipment on both sides, the wheel base 4 is arranged under the mounting plate 21, the The wheel base 4 includes a first wheel base, a second wheel base and a third wheel base, the first wheel base is arranged at the front end below the mounting plate 21, and the second wheel base and the third wheel base are arranged side by side At the ...
Embodiment 3
[0043] The following is attached Figure 1-7 , to further improve Embodiment 1, adding a harmonic reducer 10 can increase the torque of the robot and improve the carrying capacity. The robot includes a car body 2, a harmonic reducer 10, a magnetically conductive wheel 1 and a magnetic control device 3, the car body 2 is made of aluminum alloy material, and the car body 2 includes a mounting plate 21 and two cavities Body 22, the cavity 22 is welded on the left and right sides of the lower surface of the mounting plate 21, the cavity 22 is used to protect the exposed equipment on both sides, and the lower surface of the mounting plate 21 is provided with two wheel bases 4 , the magnetically permeable wheel 1 is installed on the wheel base 4 . The harmonic reducer 10 is arranged on the rotating shaft of the magnetic permeable wheel 1, one side of the harmonic reducer 10 is fixedly connected to the wheel base 4, and the other end of the harmonic reducer 10 is connected to the T...
PUM
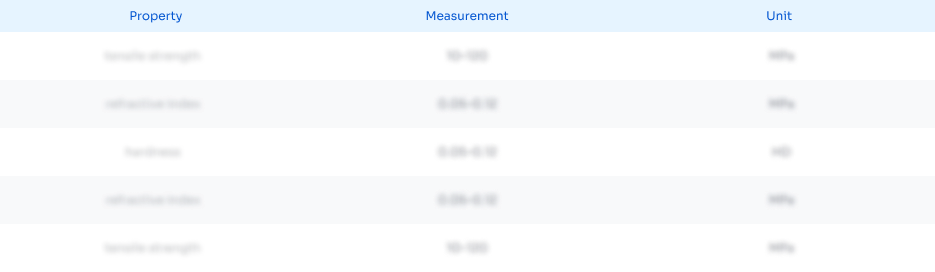
Abstract
Description
Claims
Application Information

- R&D
- Intellectual Property
- Life Sciences
- Materials
- Tech Scout
- Unparalleled Data Quality
- Higher Quality Content
- 60% Fewer Hallucinations
Browse by: Latest US Patents, China's latest patents, Technical Efficacy Thesaurus, Application Domain, Technology Topic, Popular Technical Reports.
© 2025 PatSnap. All rights reserved.Legal|Privacy policy|Modern Slavery Act Transparency Statement|Sitemap|About US| Contact US: help@patsnap.com