Method for producing oil-gas separation glass fiber filter paper through hot air drying
A technology of hot air drying and glass fiber base paper, which is applied in separation methods, filter paper, filtration separation, etc., can solve problems such as increased resistance, decreased bond strength between paper layers, and decreased porosity of paper sheets, and achieves improved filtration performance. The effect of improving the bonding strength and increasing the amount of diffusion
- Summary
- Abstract
- Description
- Claims
- Application Information
AI Technical Summary
Problems solved by technology
Method used
Image
Examples
Embodiment 1
[0013] The glass fiber base paper prepared by the conventional wet forming method is impregnated with resin and sent into a hot-air drying oven, and the paper advances in the hot-air drying oven at a paper feeding speed of 25m / min, while using 55℃-90℃ successively , 90°C-120°C, 120°C-150°C, stepwise heating hot air to dry both sides of the resin-impregnated glass fiber base paper at the same time until the moisture content is less than 5%, and the glass fiber filter paper is obtained. Among them, the resin is composed of 15 parts of phenolic resin, 1 part of curing agent PF7302B and 220 parts of methanol by weight.
Embodiment 2
[0015] The glass fiber base paper prepared by the existing conventional wet forming method is impregnated with resin and then sent into a hot air drying oven, and the paper advances in the hot air drying oven at a paper feeding speed of 40m / min, and at the same time, 55℃-90℃ , 90°C-120°C, 120°C-150°C, stepwise heating hot air to dry both sides of the resin-impregnated glass fiber base paper at the same time until the moisture content is less than 5%, and the glass fiber filter paper is obtained. Among them, the resin is composed of 14 parts of phenolic resin, 1 part of curing agent PF7302B and 220 parts of methanol by weight.
Embodiment 3
[0017] The glass fiber base paper prepared by the existing conventional wet forming method is impregnated with resin and then sent into a hot air drying oven. The paper advances in the hot air drying oven at a paper feeding speed of 34m / min. At the same time, 55℃-90℃ is adopted in sequence. , 90°C-120°C, 120°C-150°C, stepwise heating hot air to dry both sides of the resin-impregnated glass fiber base paper at the same time until the moisture content is less than 5%, and the glass fiber filter paper is obtained. Among them, the resin is composed of 16 parts of phenolic resin, 1 part of curing agent PF7302B and 220 parts of methanol by weight.
PUM
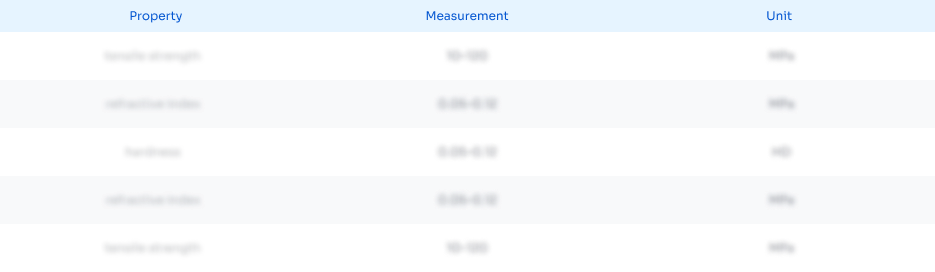
Abstract
Description
Claims
Application Information

- R&D Engineer
- R&D Manager
- IP Professional
- Industry Leading Data Capabilities
- Powerful AI technology
- Patent DNA Extraction
Browse by: Latest US Patents, China's latest patents, Technical Efficacy Thesaurus, Application Domain, Technology Topic, Popular Technical Reports.
© 2024 PatSnap. All rights reserved.Legal|Privacy policy|Modern Slavery Act Transparency Statement|Sitemap|About US| Contact US: help@patsnap.com