Method for using steel slags to prepare lightweight carbonized building material
A steel slag, lightweight technology, which is applied in the field of comprehensive utilization of resources, can solve the problems of difficult utilization of steel slag carbonized products and high preparation costs, and achieve the effects of saving transportation costs, reducing consumption and protecting the environment.
- Summary
- Abstract
- Description
- Claims
- Application Information
AI Technical Summary
Problems solved by technology
Method used
Image
Examples
Embodiment 1
[0036] Step 1. Dry the steel slag to a moisture content of 0-1%, and grind the dried steel slag to a specific surface area of 400kg / m 2 and 600kg / m 2 Two parts; and mix uniformly according to the mass ratio of 1:1 to prepare steel slag mixture; dry the gypsum to a moisture content of 0-1%, and grind the dried gypsum to a specific surface area of 650kg / m 2 ;Dry the ceramsite to a moisture content of 0-1%;
[0037] Step 2: Mix the raw materials prepared in step 1 with steel slag 56.4%, gypsum 3.6%, and ceramsite 40% by weight percentage on a dry basis to obtain a mixed dry material, and add 0.9% of the total mass of the mixed dry material to the mixed dry material. Agent and the water that accounted for 15% of the total mass of the mixed dry material were stirred for 180 seconds to obtain a mixed slurry;
[0038] Step 3: Carry out constant temperature and humidity curing for 1 day in a standard concrete curing box at 20°C and a relative humidity above 95%;
[0039] Step 4...
Embodiment 2
[0043]Step 1. Dry the steel slag to a moisture content of 0-1%, and grind the dried steel slag to a specific surface area of 400kg / m 2 and 600kg / m 2 Two parts; and mix uniformly according to the mass ratio of 1:1 to prepare steel slag mixture; dry the gypsum to a moisture content of 0-1%, and grind the dried gypsum to a specific surface area of 650kg / m 2 ;Dry the expanded perlite to a moisture content of 0-1%;
[0044] Step 2, the raw materials prepared in step 1 are prepared according to 56.4% of steel slag, 3.6% of gypsum, and 40% of expanded perlite to obtain a mixed dry material according to the dry weight percentage, and add 0.9% of the total mass of the mixed dry material to the mixed dry material. The water agent and the water accounting for 15% of the total mass of the mixed dry material were stirred for 180 seconds to obtain a mixed slurry;
[0045] Step 3: Carry out constant temperature and humidity curing for 1 day in a standard concrete curing box at 20°C and...
Embodiment 3
[0050] Step 1. Dry the steel slag to a moisture content of 0-1%, and grind the dried steel slag to a specific surface area of 400kg / m 2 and 600kg / m 2 Two parts; and mix uniformly according to the mass ratio of 1:1.5 to prepare steel slag mixture; dry the gypsum to a moisture content of 0-1%, and grind the dried gypsum to a specific surface area of 650kg / m 2 ;Dry the ceramsite to a moisture content of 0-1%;
[0051] Step 2: Mix the raw materials prepared in step 1 with 84.6% steel slag, 5.4% gypsum and 10% ceramsite according to the weight percentage on a dry basis to obtain a mixed dry material, and add water accounting for 20% of the total mass of the mixed dry material to the mixed dry material and stir 180 seconds, obtain mixed slurry;
[0052] Step 3: Carry out constant temperature and humidity curing for 1 day in a standard concrete curing box at 20°C and a relative humidity above 95%;
[0053] Step 4: Remove the mold after molding and put it into a carbonization b...
PUM
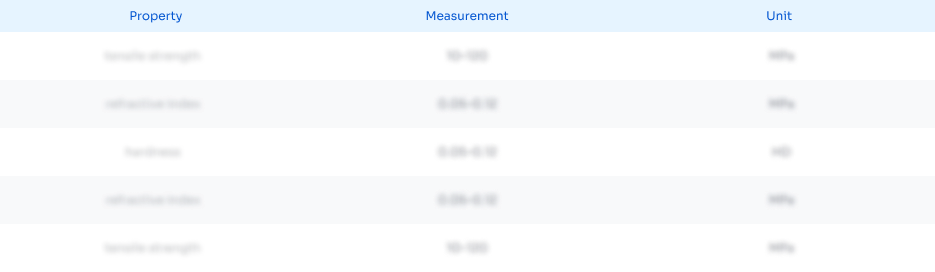
Abstract
Description
Claims
Application Information

- R&D Engineer
- R&D Manager
- IP Professional
- Industry Leading Data Capabilities
- Powerful AI technology
- Patent DNA Extraction
Browse by: Latest US Patents, China's latest patents, Technical Efficacy Thesaurus, Application Domain, Technology Topic, Popular Technical Reports.
© 2024 PatSnap. All rights reserved.Legal|Privacy policy|Modern Slavery Act Transparency Statement|Sitemap|About US| Contact US: help@patsnap.com