A thermally conductive film rewinding device
A heat-conducting film and unwinding device technology, which is applied in the direction of winding strips, transportation and packaging, thin material processing, etc., can solve problems such as uneven winding, affecting work efficiency, loose film tape, etc., and achieves simple and efficient design. Flexible and convenient edge-aligned roll-out effect
- Summary
- Abstract
- Description
- Claims
- Application Information
AI Technical Summary
Problems solved by technology
Method used
Image
Examples
Embodiment 1
[0027] Such as Figure 1-5 As shown, a thermally conductive film rewinding device includes an unwinding device 1 and a winding device 2. The unwinding device 1 includes an unwinding shaft 101, a first support frame 102 and a base 103. Bearings are provided at both ends of the unwinding shaft 101. plate 12, and the bearing plate 12 is fixed on the top of the first support frame 102 by screws, the bottom end of the first support frame 102 is welded with a base 103, and the winding device 2 includes a first rolling shaft 201, a winding shaft 202 and a second support The frame 203, the first rolling shaft 201 and the winding shaft 202 are arranged up and down in the second supporting frame 203 in a staggered manner, and the inside of the second supporting frame 203 is located above the first rolling shaft 201. The end is connected with the motor 4 by a belt, and the two ends of the base 103 are equipped with a cylinder 6, and the cylinder 6 is connected with the second support fra...
Embodiment 2
[0032] Such as Figure 1-5 The unwinding shaft 101 is welded with the first gear 8 at the part where the unwinding shaft 101 extends out of the bearing plate 12. Both sides of the first support frame 102 are connected with the second gear 9 through the resistance rotating shaft. The diameter of the first gear 8 is 5 cm, and the second gear 9 The diameter is 10cm, and the first gear 8 and the second gear 9 are engaged with each other.
[0033] The first gear 8 and the second gear 9 are set. After the motor 4 stops working, due to inertia, the unwinding 101 will continue to rotate. At this time, the first gear 8 drives the second gear 9 to rotate without external power. The friction between them and the resistance of the resistance rotating shaft offset the inertial force brought, thereby preventing the unwinding shaft 101 from continuing to rotate.
Embodiment 3
[0035] Such as Figure 1-5 As shown, the cross-sections of the unwinding shaft 101, the first rolling shaft 201 and the winding shaft 202 are all I-shaped, and the inner sides of the two ends of the unwinding shaft 101 are connected to the limit collar 10 by evenly setting 8 sets of first springs 11, which are I-shaped. The structure ensures that the thermal conductive film is neatly wrapped in each axis, thereby avoiding winding deviation to a certain extent;
[0036] The first rolling shaft 201 is erected in the second support frame 203, and the two ends of the first rolling shaft 201 are sleeved with elastic sleeves 13. When the first rolling shaft 201 rotates, the elastic sleeve 13 is on the axis of the first rolling shaft 201. Fixed and rotated, the elastic sleeve 13 is in contact with the second support frame 203, which does not affect its rotation. The first rolling shaft 201 rotates on the surface of its axis. The spring sleeve 13 is elastically deformed to deal with ...
PUM
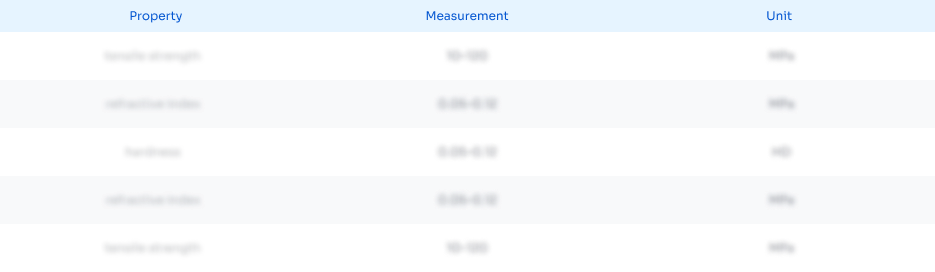
Abstract
Description
Claims
Application Information

- R&D Engineer
- R&D Manager
- IP Professional
- Industry Leading Data Capabilities
- Powerful AI technology
- Patent DNA Extraction
Browse by: Latest US Patents, China's latest patents, Technical Efficacy Thesaurus, Application Domain, Technology Topic, Popular Technical Reports.
© 2024 PatSnap. All rights reserved.Legal|Privacy policy|Modern Slavery Act Transparency Statement|Sitemap|About US| Contact US: help@patsnap.com