Fault-tolerant control method based on hidden Markov model
A fault-tolerant control and model technology, applied in the direction of adaptive control, general control system, control/regulation system, etc., can solve the problems of structural accuracy, low reliability, poor effect of model predictive control, etc.
- Summary
- Abstract
- Description
- Claims
- Application Information
AI Technical Summary
Problems solved by technology
Method used
Image
Examples
Embodiment
[0063] In this embodiment, a fault-tolerant control method based on a hidden Markov model comprises the following steps:
[0064] S1. Offline modeling, collecting training sample sets, using the offline data collected in the industrial process as the observation sequence of the hidden Markov model, and training the hidden Markov model; the specific process includes:
[0065] S11. Use a stochastic nonlinear system to describe the industrial process, and the stochastic nonlinear system is expressed by the following formula:
[0066]
[0067] Where t is the time index, and the superscript [i] represents the working condition index, Indicates the state of working condition i, n x is the number of state variables, Indicates control input, n u is the number of input variables, Indicates time-invariant model parameters, n θ is the number of model parameters, Indicates that with known finite covariance ∑ ω The zero-mean process noise of f [i] : Represents the model eq...
PUM
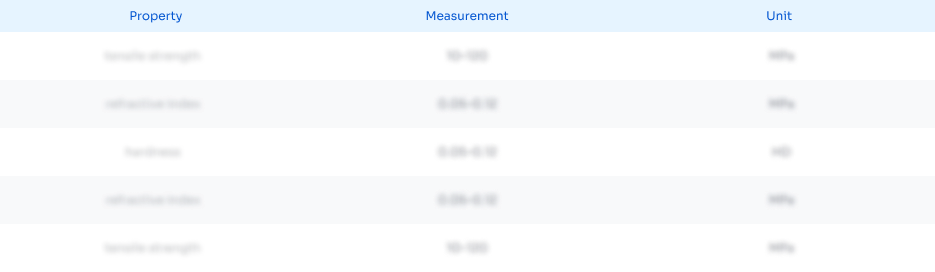
Abstract
Description
Claims
Application Information

- R&D
- Intellectual Property
- Life Sciences
- Materials
- Tech Scout
- Unparalleled Data Quality
- Higher Quality Content
- 60% Fewer Hallucinations
Browse by: Latest US Patents, China's latest patents, Technical Efficacy Thesaurus, Application Domain, Technology Topic, Popular Technical Reports.
© 2025 PatSnap. All rights reserved.Legal|Privacy policy|Modern Slavery Act Transparency Statement|Sitemap|About US| Contact US: help@patsnap.com