Six-dimensional force sensor calibration device and method
A technology of six-dimensional force sensor and calibration device, applied in the direction of measurement device, instrument, force/torque/work measuring instrument calibration/test, etc. errors, etc.
- Summary
- Abstract
- Description
- Claims
- Application Information
AI Technical Summary
Problems solved by technology
Method used
Image
Examples
Embodiment Construction
[0057] Such as figure 1 As shown, the present invention proposes a six-dimensional force sensor calibration device, the six-dimensional force sensor includes a sensor elastic body, the center of the sensor elastic body is provided with a force hole, and the six-dimensional force sensor calibration device includes a frame , a rotating mechanism, a force receiving device, a first loading device, a second loading device, a third loading device and a control system. The orientation of this manual is based on figure 1 as a benchmark, and set figure 1 The right side of the sensor elastic body in the position state is the positive direction of the x-axis, the rear side is the positive direction of the y-axis, and the upper side is the positive direction of the z-axis.
[0058] The frame includes a support platform 1 , support legs 2 and a portal bracket 3 fixed on the support platform 1 .
[0059] The rotating mechanism includes a rotating platform 4 arranged above the support pla...
PUM
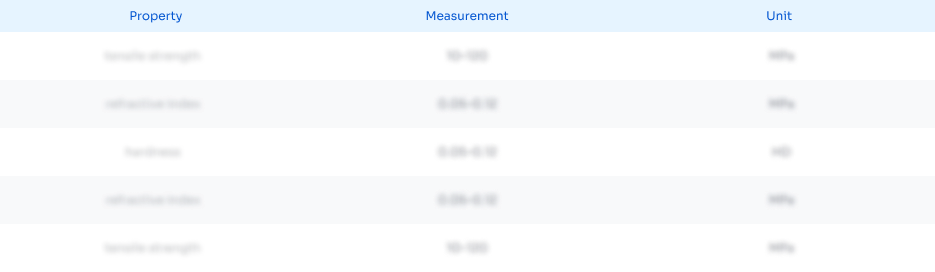
Abstract
Description
Claims
Application Information

- R&D
- Intellectual Property
- Life Sciences
- Materials
- Tech Scout
- Unparalleled Data Quality
- Higher Quality Content
- 60% Fewer Hallucinations
Browse by: Latest US Patents, China's latest patents, Technical Efficacy Thesaurus, Application Domain, Technology Topic, Popular Technical Reports.
© 2025 PatSnap. All rights reserved.Legal|Privacy policy|Modern Slavery Act Transparency Statement|Sitemap|About US| Contact US: help@patsnap.com