Forked type piezoelectric stack damping ring
A technology of piezoelectric stacking and vibration damping rings, which is applied in the direction of spring/shock absorber, vibration suppression adjustment, non-rotational vibration suppression, etc., can solve problems such as difficult installation and processing, poor environmental adaptability, short service life, etc. Rapid, reduced size and weight, highly robust results
- Summary
- Abstract
- Description
- Claims
- Application Information
AI Technical Summary
Problems solved by technology
Method used
Image
Examples
Embodiment Construction
[0024] The present invention will be further described below in conjunction with accompanying drawing.
[0025] The present invention is installed between bearings and supports, gears and shafts in the rotor system, such as image 3 shown. It is mainly used to reduce the output force to the support caused by vibration, thereby reducing the vibration response of the overall structure. The fork-shaped protection frame of the vibration damping ring can protect the piezoelectric stack from being damaged by tangential force and torque, and improve the service life and stability of the piezoelectric stack.
[0026] The structure of the present invention is as Figure 8 As shown, it includes a piezoelectric stack 1, a fork-shaped protective frame 2, an outer ring 3 and an external shunt circuit 5, wherein the fork-shaped protective frame 2 is set on the bearing 4, the fork-shaped protective frame 2 is covered with an outer ring 3, and the outer ring 3 Tightly hooped on the fork-sh...
PUM
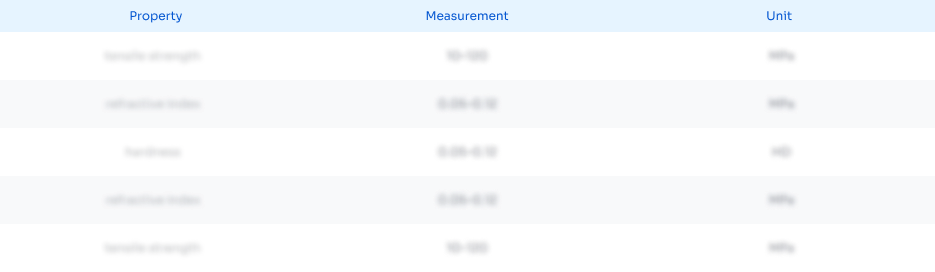
Abstract
Description
Claims
Application Information

- R&D
- Intellectual Property
- Life Sciences
- Materials
- Tech Scout
- Unparalleled Data Quality
- Higher Quality Content
- 60% Fewer Hallucinations
Browse by: Latest US Patents, China's latest patents, Technical Efficacy Thesaurus, Application Domain, Technology Topic, Popular Technical Reports.
© 2025 PatSnap. All rights reserved.Legal|Privacy policy|Modern Slavery Act Transparency Statement|Sitemap|About US| Contact US: help@patsnap.com