Process for removing sodium chloride from salt mud produced in chlor-alkali production
A technology of sodium chloride and salt mud, which is applied in cement production, horticulture, sludge treatment, etc., can solve the problems of unqualified discharge, inability to be washed by sodium chloride, inability to be directly discharged or utilized, etc., to reduce discharge pressure, The effect of meeting the requirements of cleaner production
- Summary
- Abstract
- Description
- Claims
- Application Information
AI Technical Summary
Problems solved by technology
Method used
Examples
Embodiment 1
[0022] 1) Mix the saline mud brine with 0.8% polyacrylamide aqueous solution (flocculant) of the saline mud brine quality and send it to the automatic centrifuge to separate the salt mud from the brine, collect the brine and return it to be used as salt, and the salt mud Collect and put into the salt washing tank to be washed with water to remove the salt;
[0023] 2) According to the amount of salt mud and salt water in the mud washing tank, add a certain amount of water to stir and wash. The solution composition in the salt washing tank is: salt mud: water: salt = 13.5: 84.5: 2;
[0024] 3) Transfer the above solution to a plate and frame filter press (press filter pressure 0.8MPa, filter press time 120min), discharge after press filter, and collect;
[0025] 4) Collect the discharged salt mud, take samples for analysis, and send them to the cement factory to use as raw materials for cement production or plant cultivation after passing the test.
Embodiment 2
[0027] 1) Mix the saline mud brine with 1.1% polyacrylamide aqueous solution containing saline mud brine and send it to the automatic centrifuge. The salt mud and brine are separated, and the brine is collected and returned to the salt. Add water to wash and remove salt in the salt pond;
[0028] 2) According to the amount of salt mud and salt water in the mud washing tank, add a certain amount of water to stir and wash. The solution composition in the salt washing tank is: salt mud: water: salt = 13:85:2;
[0029] 3) Transfer the above solution to a plate-and-frame filter press (press filter pressure 0.82MPa, press filter time 121min), discharge after press filter, and collect;
[0030] 4) Collect the discharged salt mud, take samples for analysis, and send them to the cement factory to use as raw materials for cement production or plant cultivation after passing the test.
Embodiment 3
[0032] 1) Mix the saline mud brine with 0.6% polyacrylamide aqueous solution containing saline mud brine and send it to the automatic centrifuge, the salt mud is separated from the brine, the brine is collected and returned to the salt, and the salt mud is collected and put into the washing machine Add water to wash and remove salt in the salt pond;
[0033] 2) According to the amount of salt mud and salt water in the mud washing tank, add a certain amount of water to stir and wash. The solution composition in the salt washing tank is: salt mud: water: salt = 14:84:2;
[0034] 3) Transfer the above solution to a plate-and-frame filter press (press filter pressure 0.78 MPa, filter press time 125min), discharge after press filter, and collect;
[0035] 4) Collect the discharged salt mud, take samples for analysis, and send them to the cement factory to use as raw materials for cement production or plant cultivation after passing the test.
PUM
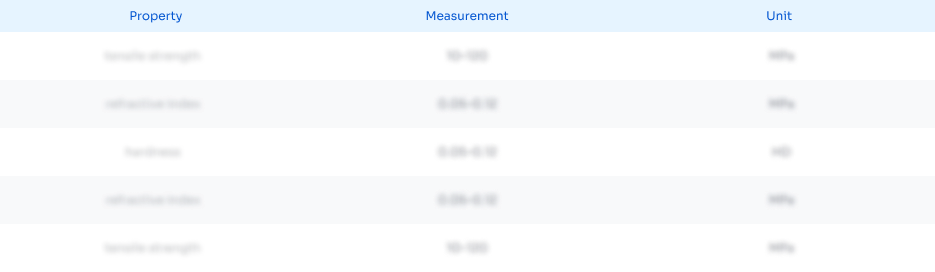
Abstract
Description
Claims
Application Information

- R&D Engineer
- R&D Manager
- IP Professional
- Industry Leading Data Capabilities
- Powerful AI technology
- Patent DNA Extraction
Browse by: Latest US Patents, China's latest patents, Technical Efficacy Thesaurus, Application Domain, Technology Topic, Popular Technical Reports.
© 2024 PatSnap. All rights reserved.Legal|Privacy policy|Modern Slavery Act Transparency Statement|Sitemap|About US| Contact US: help@patsnap.com