Method and tool for calibration of hollow profile component produced by extrusion for automobile manufacturing
A technology of extrusion processing of hollow profiles, applied in the direction of manufacturing tools, forming tools, vehicle parts, etc., can solve the problems of hollow profile size and shape deviation, and achieve the effect of short cycle time and small shape error
- Summary
- Abstract
- Description
- Claims
- Application Information
AI Technical Summary
Problems solved by technology
Method used
Image
Examples
Embodiment Construction
[0049] figure 1 The hollow profile member 100 shown in the figure is composed of an aluminum rectangular profile that is extruded. The hollow profile component 100 can have an axial length of, for example, 1000 mm and be assembled as a longitudinal beam or a cross beam in a motor vehicle, for example as a component of the body space frame structure. Based on the manufacturing method of extrusion processing, the hollow profile member 100 may have size and shape deviations, such as twisted or bent forms, and thus need to be finished before assembly, especially in view of the joining technology used.
[0050] figure 2 Shown is a stamping die 200 for finishing the hollow profile member 100 of the present invention. The stamping die 200 installed in the forming press includes a lower die 210 configured as a forming die. The figure only shows the working surface of the lower die and the upper die 220 configured as a die. The upper die is also only Show its active surface. The struc...
PUM
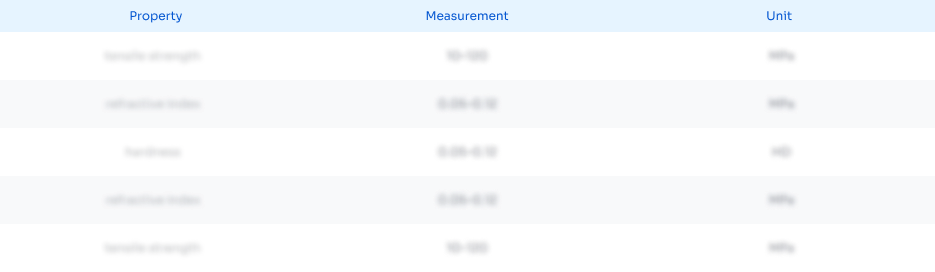
Abstract
Description
Claims
Application Information

- R&D
- Intellectual Property
- Life Sciences
- Materials
- Tech Scout
- Unparalleled Data Quality
- Higher Quality Content
- 60% Fewer Hallucinations
Browse by: Latest US Patents, China's latest patents, Technical Efficacy Thesaurus, Application Domain, Technology Topic, Popular Technical Reports.
© 2025 PatSnap. All rights reserved.Legal|Privacy policy|Modern Slavery Act Transparency Statement|Sitemap|About US| Contact US: help@patsnap.com