Sandwiched type piezoelectric manipulator based on spherical joint and control method of manipulator
A technology of spherical joints and manipulators, applied in the field of manipulators, can solve the problems of small mass, volume, power density, difficult miniaturization design, unfavorable miniaturization, etc., and achieve the effect of simple and compact structure, smart functions, and easy miniaturization
- Summary
- Abstract
- Description
- Claims
- Application Information
AI Technical Summary
Problems solved by technology
Method used
Image
Examples
Embodiment Construction
[0035] Below in conjunction with accompanying drawing, technical scheme of the present invention is described in further detail:
[0036] Such as figure 1 As shown, the present invention discloses a sandwich-type piezoelectric manipulator based on spherical joints, including a palm platform 1 and at least two fingers 2 .
[0037] Such as figure 2 As shown, each finger is composed of a first joint 3, a first phalanx 4, a second joint 5 and a terminal phalanx 6; the first joint 3 of each finger is connected to the palm platform 1 by bolts.
[0038] Such as image 3 As shown, the first joint 3 and the second joint 5 are composed of a first ring vibrator 8, a second ring vibrator 12, a support frame 10, and several bolts, elastic washers, and nuts. The first ring vibrator, the second The ring vibrator is installed in the stepped groove, and the bolt passes through the positioning hole of the counterweight of the first ring vibrator, the elastic washer, and the support frame, a...
PUM
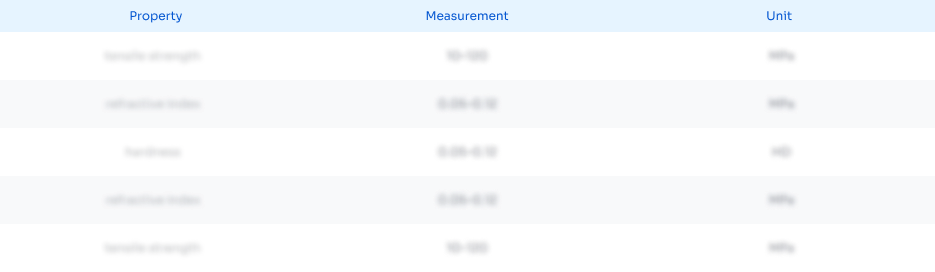
Abstract
Description
Claims
Application Information

- R&D
- Intellectual Property
- Life Sciences
- Materials
- Tech Scout
- Unparalleled Data Quality
- Higher Quality Content
- 60% Fewer Hallucinations
Browse by: Latest US Patents, China's latest patents, Technical Efficacy Thesaurus, Application Domain, Technology Topic, Popular Technical Reports.
© 2025 PatSnap. All rights reserved.Legal|Privacy policy|Modern Slavery Act Transparency Statement|Sitemap|About US| Contact US: help@patsnap.com