Machining technology of sheet for H-shaped long beam
A processing technology and long beam technology, which is applied in the field of processing technology for H-shaped long beams, can solve the problems of high maintenance cost and poor adjustability, and achieve the effects of low maintenance cost, easy maintenance and strong adjustability
- Summary
- Abstract
- Description
- Claims
- Application Information
AI Technical Summary
Problems solved by technology
Method used
Image
Examples
Embodiment 1
[0048] See Figure 1 to Figure 5 , A processing technique for a plate used on an H-shaped long beam. The processing technique includes the following steps: first transport the metal sheet 1 to be processed to the plate feeding unit 5, and then drive the plate feeding pusher 52 along the plate feeding slot 51 Perform a horizontal movement to push the metal sheet 1 to be processed onto the cutting unit 2, and then adjust the strip support seats 21 in the cutting unit 2 to change the distribution of the strip support seats 21 below the metal sheet 1 Density and the distance between the top end of each long strip support seat 21 and the bottom surface of the metal sheet 1. The adjustment operation includes the horizontal movement and vertical movement of the long strip support seat 21. After the adjustment operation is completed, it is suspended above the cutting unit 2 The cutting machine performs a cutting operation on the metal sheet 1.
[0049] The special equipment for the abov...
Embodiment 2
[0051] The basic content is the same as Example 1, the difference is:
[0052] The elongated base 22 is a hollow structure, and a coaxial elongated cavity 221 is opened inside the elongated base 22. One end of the elongated cavity 221 is flush with the end surface of the elongated base 22, and the elongated cavity The other end of 221 is connected with the intake pipe head 222; the plastic ball seat 27 includes a spherical surface 28 and a fixing portion 29, the side circumference of the spherical surface 28 is a spherical structure, and a plurality of The vent hole 272, the top end of the spherical surface 28 is connected with the bottom end of the metal ball 26, the bottom end of the spherical surface 28 is connected with the top end of the fixing portion 29, and the bottom end of the fixing portion 29 passes through the top surface of the elongated base 22 In contact with the elongated cavity 221, the spherical surface 28 is provided with a spherical cavity 281 communicating w...
Embodiment 3
[0054] The basic content is the same as in Example 2, the difference is:
[0055] The spherical cavity 281 includes a hemispherical cavity 282 and a truncated cone cavity 283. The bottom of the hemispherical cavity 282 is communicated with the top of the fixed cavity 291 after passing through the truncated cone cavity 283. The top of the truncated cone cavity 283 is wider than its bottom. The vent hole 272 is arranged along the cross line of the hemispherical cavity 282 and the truncated cone cavity 283. Preferably, the side circumference of the spherical portion 28 has an elliptical spherical structure.
PUM
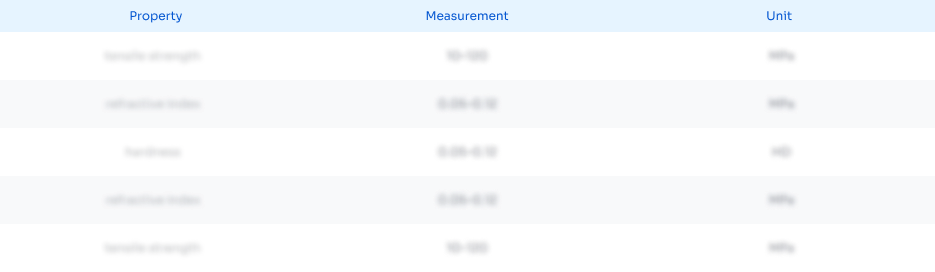
Abstract
Description
Claims
Application Information

- R&D Engineer
- R&D Manager
- IP Professional
- Industry Leading Data Capabilities
- Powerful AI technology
- Patent DNA Extraction
Browse by: Latest US Patents, China's latest patents, Technical Efficacy Thesaurus, Application Domain, Technology Topic, Popular Technical Reports.
© 2024 PatSnap. All rights reserved.Legal|Privacy policy|Modern Slavery Act Transparency Statement|Sitemap|About US| Contact US: help@patsnap.com