Double-beam laser mirror image welding method
A welding method and double-beam technology, applied in laser welding equipment, welding equipment, metal processing equipment, etc., can solve the problems of low process manufacturing efficiency, inconvenient operation of turning the rudder surface, inconvenient automatic welding, etc., to ensure the symmetry of temperature changes , Improve welding efficiency and facilitate automation
- Summary
- Abstract
- Description
- Claims
- Application Information
AI Technical Summary
Problems solved by technology
Method used
Image
Examples
Embodiment Construction
[0037] The present invention will be described in detail below in conjunction with specific embodiments. The following examples will help those skilled in the art to further understand the present invention, but do not limit the present invention in any form. It should be noted that those skilled in the art can make several changes and improvements without departing from the concept of the present invention. These all belong to the protection scope of the present invention.
[0038] According to a double-beam laser image welding method provided by the present invention, the first part and the second part to be welded are used, including the following steps:
[0039] Welding preparation step: pretreatment of the first part and the second part;
[0040] Fixing step: performing combined mechanical assembly and spot welding of the first component and the second component;
[0041] Welding step: the first part and the second part are welded through formal laser welding;
[0042...
PUM
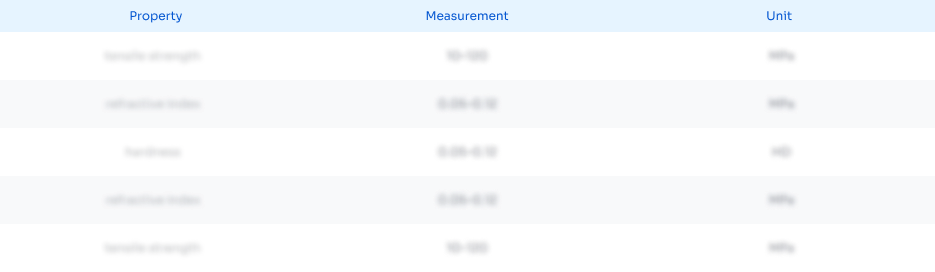
Abstract
Description
Claims
Application Information

- Generate Ideas
- Intellectual Property
- Life Sciences
- Materials
- Tech Scout
- Unparalleled Data Quality
- Higher Quality Content
- 60% Fewer Hallucinations
Browse by: Latest US Patents, China's latest patents, Technical Efficacy Thesaurus, Application Domain, Technology Topic, Popular Technical Reports.
© 2025 PatSnap. All rights reserved.Legal|Privacy policy|Modern Slavery Act Transparency Statement|Sitemap|About US| Contact US: help@patsnap.com