Alcohol-based coating for cast iron stove and preparation method of alcohol-based coating
An alcohol-based and stove technology, which is applied to casting molding equipment, coatings, casting molds, etc., can solve the problems of easy volatility, poor advection, and poor suspension, and achieve improved permeability, improved bonding performance, and anti-sticking sand good performance
- Summary
- Abstract
- Description
- Claims
- Application Information
AI Technical Summary
Problems solved by technology
Method used
Examples
Embodiment 1
[0018] An alcohol-based coating for cast iron stoves, comprising the following raw materials in parts by weight: 30 parts of epoxy resin, 15 parts of glass fiber, 4 parts of borax, 3 parts of nano silicon dioxide, 10 parts of modified starch, 30 parts of pentaerythritol and 30 parts of isoamyl alcohol.
[0019] Put pentaerythritol and glass fiber in ultrasonic wave to disperse evenly to obtain dispersion A, place borax, nano-silica and isoamyl alcohol in ultrasonic wave to disperse evenly to obtain dispersion B, add dispersion A in turn under stirring condition Epoxy resin, dispersion B and binder, mixed evenly to obtain alcohol-based paint.
[0020] The modified starch is obtained through the following steps: mix the starch with water, heat to 60-80°C, add citric acid after mixing well, cool down to 30-40°C, keep the temperature at 30-40°C, add α- Amylase reacts for 30-60 minutes under stirring conditions, then adds acrylic acid and polyglycerin fatty acid ester, and stirs t...
Embodiment 2
[0023] An alcohol-based coating for cast iron stoves, comprising the following raw materials in parts by weight: 40 parts of epoxy resin, 10 parts of glass fiber, 8 parts of borax, 1 part of nano silicon dioxide, 15 parts of modified starch, 40 parts of pentaerythritol and 40 parts of isoamyl alcohol.
[0024] Put pentaerythritol and glass fiber in ultrasonic wave to disperse evenly to obtain dispersion A, place borax, nano-silica and isoamyl alcohol in ultrasonic wave to disperse evenly to obtain dispersion B, add dispersion A in turn under stirring condition Epoxy resin, dispersion B and binder, mixed evenly to obtain alcohol-based paint.
[0025] The modified starch is obtained through the following steps: mix the starch with water, heat to 60-80°C, add citric acid after mixing well, cool down to 30-40°C, keep the temperature at 30-40°C, add α- Amylase reacts for 30-60 minutes under stirring conditions, then adds acrylic acid and polyglycerin fatty acid ester, and stirs th...
Embodiment 3
[0028] An alcohol-based coating for cast iron stoves, comprising the following raw materials in parts by weight: 36 parts of epoxy resin, 12 parts of glass fiber, 5 parts of borax, 2 parts of nano silicon dioxide, 13 parts of binder, 35 parts of pentaerythritol and 35 parts of isoamyl alcohol.
[0029] Put pentaerythritol and glass fiber in ultrasonic wave to disperse evenly to obtain dispersion A, place borax, nano-silica and isoamyl alcohol in ultrasonic wave to disperse evenly to obtain dispersion B, add dispersion A in turn under stirring condition Epoxy resin, dispersion B and binder, mixed evenly to obtain alcohol-based paint.
[0030] The binder is modified starch. The modified starch is obtained through the following steps: mix the starch with water, heat to 60-80°C, add citric acid after mixing well, cool down to 30-40°C, keep the temperature at 30-40°C, add α- Amylase reacts for 30-60 minutes under stirring conditions, then adds acrylic acid and polyglycerin fatty ...
PUM
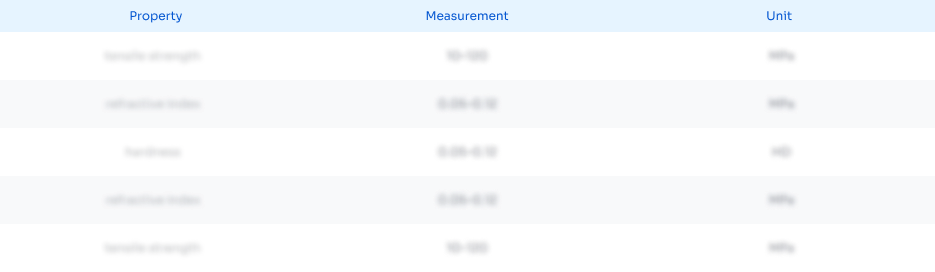
Abstract
Description
Claims
Application Information

- Generate Ideas
- Intellectual Property
- Life Sciences
- Materials
- Tech Scout
- Unparalleled Data Quality
- Higher Quality Content
- 60% Fewer Hallucinations
Browse by: Latest US Patents, China's latest patents, Technical Efficacy Thesaurus, Application Domain, Technology Topic, Popular Technical Reports.
© 2025 PatSnap. All rights reserved.Legal|Privacy policy|Modern Slavery Act Transparency Statement|Sitemap|About US| Contact US: help@patsnap.com