Self-pressurizing fuel tanks for space propulsion
A technology for space propulsion and fuel tanks, applied in spaceflight vehicle propulsion system devices, spaceflight equipment, spaceflight vehicles, etc., can solve problems such as unfavorable spacecraft temperature control, and achieve favorable temperature control, structure and work Simple principle, constant thrust effect
- Summary
- Abstract
- Description
- Claims
- Application Information
AI Technical Summary
Problems solved by technology
Method used
Image
Examples
Embodiment 1
[0040] This embodiment is used for a self-pressurized fuel tank for space propulsion, such as Image 6 As shown, it includes: housing 1, piston 2, upper cover 3, screw nut mechanism 4, motor-bevel gear group 5, disc spring group 6, pipe 7, one end of the housing is connected to the pipe, and the other end is connected to the screw nut mechanism The upper cover 3, the disc spring group 6, and the piston 2 are arranged in the shell from top to bottom. The shell located in the lower space of the piston is filled with liquid fuel. A disc spring group is arranged between the piston and the upper cover. The upper end of the spring group 6 is close to the lower end surface of the upper cover, and the lower end of the disc spring group 6 is close to the bottom surface of the inner wall of the piston 2; a screw nut mechanism is connected between the upper cover and the housing, and the screw nut mechanism is connected to the motor at the same time- The bevel gear set, the motor-bevel gea...
Embodiment 2
[0045] The motor-bevel gear set of the fuel tank of this embodiment is installed in the upper cover, and the installation method is exactly the same as that in the first embodiment; the installation method and function of the screw nut are also the same as the first embodiment. The difference from Example 1 is the piston and upper cover (see Picture 9 ). The piston of this embodiment (see Picture 10 ) It should be close to the non-circular inner wall of the shell, and there should be a circular guide post on the piston to install the disc spring assembly. Upper cover (see Picture 11 ) A concave round sleeve is sleeved on the circular guide post of the piston, and the upper edge of the upper cover should also be close to the non-circular inner wall of the shell. The outer diameter of the concave round sleeve is larger than the radius of the disc spring.
Embodiment 3
[0047] The fuel tank of this embodiment (see Picture 12 The motor-bevel gear set of) is installed in the upper cover, and the installation method is exactly the same as that in Embodiment 2. The installation method and function of the screw nut are also the same as in Embodiment 2. Piston (see Figure 13 ) It should be close to the non-circular inner wall of the shell, the piston is concave, and there should be a circular guide post on the piston, and a disc spring group should be installed on the circular guide post. Upper cover (see Figure 14 ) There is a concave round sleeve sleeved on the circular guide post of the piston. The difference from Embodiment 2 is that the upper edge of the upper cover must be close to the concave inner wall of the piston. The outer diameter of the concave round sleeve is larger than the radius of the disc spring.
PUM
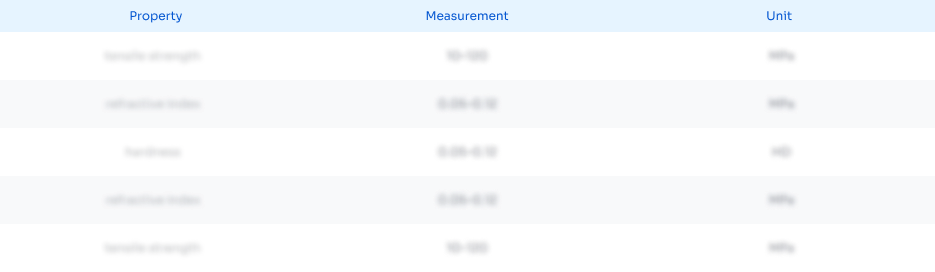
Abstract
Description
Claims
Application Information

- R&D
- Intellectual Property
- Life Sciences
- Materials
- Tech Scout
- Unparalleled Data Quality
- Higher Quality Content
- 60% Fewer Hallucinations
Browse by: Latest US Patents, China's latest patents, Technical Efficacy Thesaurus, Application Domain, Technology Topic, Popular Technical Reports.
© 2025 PatSnap. All rights reserved.Legal|Privacy policy|Modern Slavery Act Transparency Statement|Sitemap|About US| Contact US: help@patsnap.com