The structure of the feeding part of the steel pipe flaw detection
A technology of feeding part and steel pipe, which is applied in the direction of material analysis by electromagnetic means, material analysis, and material analysis by using sound wave/ultrasonic wave/infrasonic wave, etc. It can solve the problems of probe vibration, warping, signal amplitude change, etc., and achieve Good straightening effect, simple structure, and the effect of improving the effect of flaw detection
- Summary
- Abstract
- Description
- Claims
- Application Information
AI Technical Summary
Problems solved by technology
Method used
Image
Examples
Embodiment Construction
[0049] The present invention will be further described in detail below in combination with a steel pipe flaw detection system adopting the structure of the present invention and the accompanying drawings.
[0050] During specific implementation: if Figure 1 to Figure 10 shown.
[0051] A steel pipe flaw detection system, including a base plate, on which a steel pipe transmission device 1 for driving the steel pipe to move along the axis direction and a steel pipe flaw detection device 2 arranged on the steel pipe movement path are arranged on the bottom plate, and a steel pipe feeding straightening device arranged on the bottom plate Device 3, steel pipe feeding and straightening device 3 is arranged at the feeding end of the steel pipe transmission device and is used for straightening the steel pipe.
[0052] In this way, the steel pipe is straightened first and then the material is fed for flaw detection, which can better avoid the influence of the straightness or surface ...
PUM
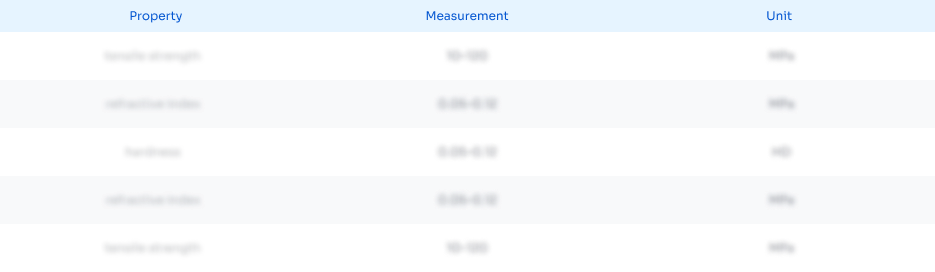
Abstract
Description
Claims
Application Information

- R&D Engineer
- R&D Manager
- IP Professional
- Industry Leading Data Capabilities
- Powerful AI technology
- Patent DNA Extraction
Browse by: Latest US Patents, China's latest patents, Technical Efficacy Thesaurus, Application Domain, Technology Topic, Popular Technical Reports.
© 2024 PatSnap. All rights reserved.Legal|Privacy policy|Modern Slavery Act Transparency Statement|Sitemap|About US| Contact US: help@patsnap.com