Straw-steel system prefabricated wall and joint connecting method
A prefabricated and wall technology, applied in walls, building components, buildings, etc., can solve the problems of rivet connection cost, steel and labor, etc., and achieve the effect of ensuring performance and use requirements, good fireproof and waterproof performance, and easy installation
- Summary
- Abstract
- Description
- Claims
- Application Information
AI Technical Summary
Problems solved by technology
Method used
Image
Examples
Embodiment 1
[0041] A straw-steel system fabricated wall, which consists of a set of straw boards 1, and the joints of the two sides of the straw boards are L-shaped structure, 6-shaped structure or 9-shaped structure. The straw boards are connected to form an L-shaped wall or a T-shaped wall or a cross-shaped wall. The upper and lower sides of the straw boards are covered with C-shaped steel sleeves 2, and the inflection points of the straw boards pass through the L-shaped steel 14 and In the C-shaped steel sleeve welding, the straw slabs are welded to the C-shaped steel sleeve through the strip steel plate where there is no inflection point, and the cross-shaped area in the middle of the straw slabs intersects is welded with the light steel plate 4 The C-shaped steel sleeve welding, the light steel plate is the steel plate used for the tic-tack grid in the outer steel frame of the straw plate, the straw plate, the C-shaped steel sleeve, the L-shaped steel, the strip steel plate, the The o...
Embodiment 2
[0047] A manufacturing method of fabricated wall using the straw-steel system of claim 1, the method comprising the following steps:
[0048] (1) The prefabricated straw board 1 is a fibrous material made of crop straws, and cemented materials are added to make a mixture, which is compressed and molded by a mold. The thickness of the straw board is equal to the width of the channel steel groove selected;
[0049] (2) The channel steel adopts C-shaped steel 2. The length of the C-shaped steel at the upper and lower ends of the wall is equal to the width of the wall. The length of the C-shaped steel at the upper and lower ends of each node is equal to the length of the wall plus the length of the node, and the remaining C The length of the profiled steel is equal to the length of the wall; firstly place the C-shaped steel horizontally on the ground during processing. According to the layout of the wall, the flanges and webs of the part of the C-shaped steel need to be cut to facilitat...
PUM
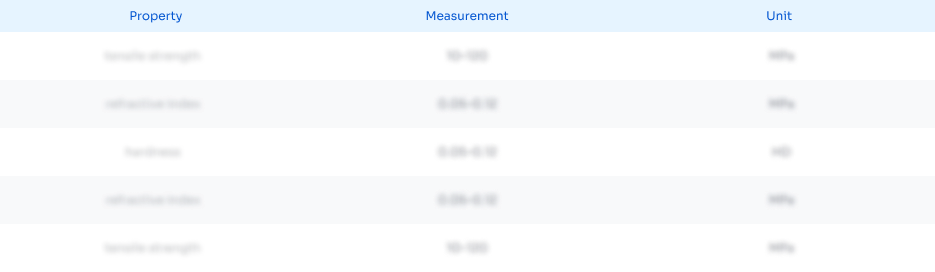
Abstract
Description
Claims
Application Information

- R&D
- Intellectual Property
- Life Sciences
- Materials
- Tech Scout
- Unparalleled Data Quality
- Higher Quality Content
- 60% Fewer Hallucinations
Browse by: Latest US Patents, China's latest patents, Technical Efficacy Thesaurus, Application Domain, Technology Topic, Popular Technical Reports.
© 2025 PatSnap. All rights reserved.Legal|Privacy policy|Modern Slavery Act Transparency Statement|Sitemap|About US| Contact US: help@patsnap.com