Novel spheroidizing annealing technology for bearing steel wire
A technology of spheroidizing annealing and steel wire, which is applied in furnace types, manufacturing tools, furnaces, etc., can solve the problems of long process cycle and annealing capacity compression, and achieve the effect of increasing annealing capacity and shortening annealing cycle.
- Summary
- Abstract
- Description
- Claims
- Application Information
AI Technical Summary
Problems solved by technology
Method used
Image
Examples
Embodiment 1
[0024] A new type of bearing steel wire spheroidizing annealing process, using a bell furnace for spheroidizing treatment, including the following steps:
[0025] A. Put the bearing steel wire in the bell-type furnace, fill the heat treatment furnace with nitrogen with a purity of 99.999% purified by a nitrogen purification device, and after 20 minutes, close the process nitrogen, and fill the heat treatment furnace with a purity of 99.999% % of industrial hydrogen, first heated to 800°C and kept for 40 minutes, and at the same time shut down the process hydrogen, then heated to the holding section, soaked at 780°C, and held for 7 hours;
[0026] B. Cooling in the first stage: Cool the temperature in the furnace to 700-720°C at a rate of 50°C / h, and keep it warm for 1h;
[0027] C. Second-stage cooling: continue to cool the furnace temperature to 650°C at a rate of 12.5°C / h;
[0028] D. The third stage of cooling: continue to cool the temperature in the furnace to 300°C at a ...
PUM
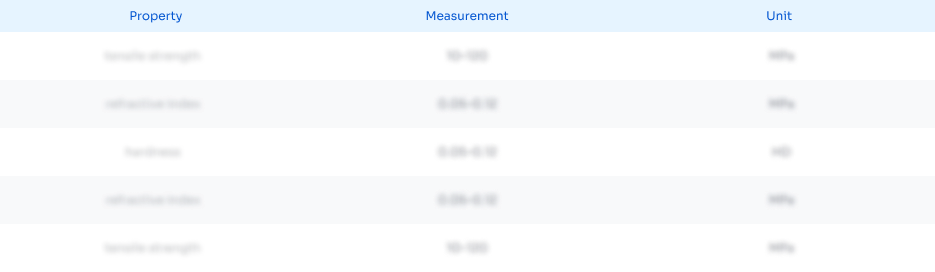
Abstract
Description
Claims
Application Information

- R&D
- Intellectual Property
- Life Sciences
- Materials
- Tech Scout
- Unparalleled Data Quality
- Higher Quality Content
- 60% Fewer Hallucinations
Browse by: Latest US Patents, China's latest patents, Technical Efficacy Thesaurus, Application Domain, Technology Topic, Popular Technical Reports.
© 2025 PatSnap. All rights reserved.Legal|Privacy policy|Modern Slavery Act Transparency Statement|Sitemap|About US| Contact US: help@patsnap.com