Manufacturing method of separator for fuel cell
A technology for fuel cells and manufacturing methods, applied to fuel cell components, fuel cells, collectors/separators, etc., capable of solving problems such as changes in the shape and position of metal plates
- Summary
- Abstract
- Description
- Claims
- Application Information
AI Technical Summary
Problems solved by technology
Method used
Image
Examples
Embodiment Construction
[0023] figure 1 is an exploded perspective view of a unit cell 2 of the fuel cell 1 . The fuel cell 1 is constructed by stacking unit cells 2 . figure 1 Only one single cell 2 is shown, and the other single cells are omitted. Single battery 2 in figure 1 Stacked with other single cells in the Z direction shown. The unit cells 2 have a substantially rectangular shape. The longitudinal direction and the short direction of the single battery 2 correspond to figure 1 The Y and X directions shown in .
[0024] The fuel cell 1 is a polymer electrolyte fuel cell that generates electricity using a fuel gas (such as hydrogen) and an oxidant gas (such as oxygen) as reaction gases. The single cell 2 comprises: a membrane electrode gas diffusion layer assembly 10 (hereinafter referred to as MEGA (membrane electrode gas diffusion layer assembly)); a support frame 18 supporting the MEGA 10; a cathode separator 20 and an anode separator 40 ( Hereinafter referred to as separator). MEG...
PUM
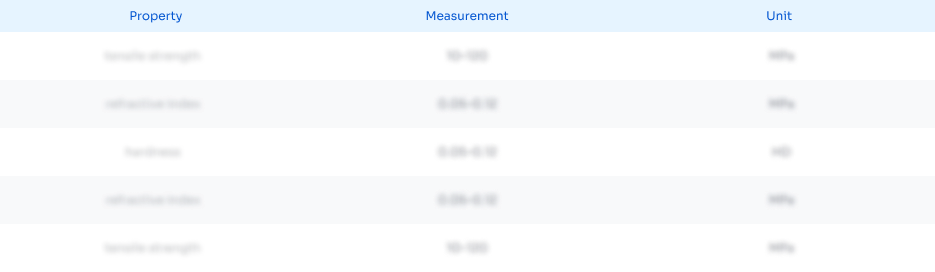
Abstract
Description
Claims
Application Information

- R&D
- Intellectual Property
- Life Sciences
- Materials
- Tech Scout
- Unparalleled Data Quality
- Higher Quality Content
- 60% Fewer Hallucinations
Browse by: Latest US Patents, China's latest patents, Technical Efficacy Thesaurus, Application Domain, Technology Topic, Popular Technical Reports.
© 2025 PatSnap. All rights reserved.Legal|Privacy policy|Modern Slavery Act Transparency Statement|Sitemap|About US| Contact US: help@patsnap.com