High-purity MTBE production process
A production process, high-purity technology, applied in the chemical industry, ether separation/purification, sustainable manufacturing/processing, etc., can solve the problems of long production process, poor economy, shortening, etc., to simplify the production process, expand Field of application, effect of reducing the number of trays
- Summary
- Abstract
- Description
- Claims
- Application Information
AI Technical Summary
Problems solved by technology
Method used
Image
Examples
Embodiment 1
[0058] The composition of C4 raw materials is shown in Table 1, and methanol is the first grade product. In the production process of high-purity MTBE, reactor 2 uses cation exchange resin as the catalyst, the molar ratio of alcohol / olefin is 1.1, the volume space velocity of the catalyst is 1.5, the reaction pressure is 0.6atm, and the reaction temperature is 50°C; catalytic rectification Tower 4 uses cation exchange resin as a catalyst, the alcohol / olefin molar ratio is 1.2, the volume space velocity of the catalyst is 1.0, the tower top pressure is 0.6-0.7atm, and the reaction temperature is 65°C; the reflux ratio of rectification tower 5 is 3.5 , the number of theoretical plates is 20, the adsorbent of the VI adsorption reactor is modified 5A molecular sieve, the space velocity is 10, the temperature is 40°C, and the pressure is 0.8MPa. The composition of MTBE products at different positions is shown in Table 2.
[0059] Table 1 C4 raw material composition wt%
[0060] ...
Embodiment 2
[0068] The composition of C4 raw materials is shown in Table 1, and methanol is a superior product. In the production process of high-purity MTBE, reactor 2 uses cation exchange resin as the catalyst, the molar ratio of alcohol / olefin is 1.05, the volume space velocity of the catalyst is 2.0, the reaction pressure is 0.6atm, and the reaction temperature is 52°C; catalytic rectification Tower 4 uses cation exchange resin as a catalyst, the alcohol / olefin molar ratio is 1.25, the volume space velocity of the catalyst is 1.2, the tower top pressure is 0.6-0.7atm, and the reaction temperature is 55°C; the reflux ratio of rectification tower 5 is 3.5 , the number of theoretical plates is 12; the adsorbent of the VI adsorption reactor is modified 5A molecular sieve, the space velocity is 13, the temperature is 40°C, and the pressure is 0.8MPa. The composition of MTBE products at different positions is shown in Table 3.
[0069] Table 3 Composition wt% of MTBE products in different p...
Embodiment 3
[0076] The composition of C4 raw materials is shown in Table 1, and methanol is the first grade product. In the production process of high-purity MTBE, the reactor 2 uses molecular sieve as the catalyst, the molar ratio of alcohol / olefin is 1.05, the volume space velocity of the catalyst is 1.0, the reaction pressure is 0.6atm, and the reaction temperature is 60°C; the catalytic rectification tower 4 Molecular sieve is used as the catalyst, the molar ratio of alcohol / olefin is 1.15, the volume space velocity of the catalyst is 0.5, the tower top pressure is 0.6-0.7atm, the reaction temperature is 65°C; the reflux ratio of rectification tower 5 is 4.5, and the number of theoretical plates The adsorbent of the VI adsorption reactor is modified 5A molecular sieve, the space velocity is 8, the temperature is 40°C, and the pressure is 0.7MPa. The composition of MTBE products at different positions is shown in Table 4.
[0077] Table 4 The composition wt% of MTBE products in differe...
PUM
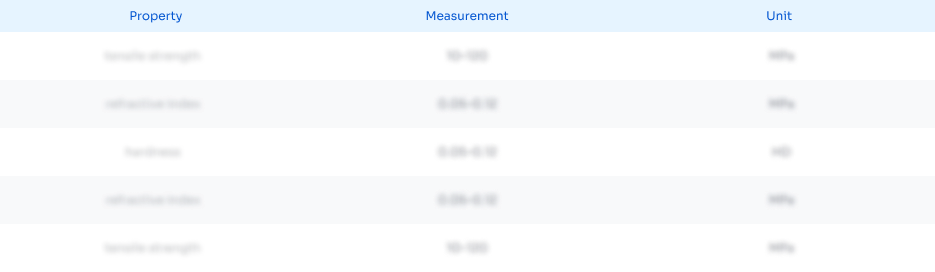
Abstract
Description
Claims
Application Information

- R&D Engineer
- R&D Manager
- IP Professional
- Industry Leading Data Capabilities
- Powerful AI technology
- Patent DNA Extraction
Browse by: Latest US Patents, China's latest patents, Technical Efficacy Thesaurus, Application Domain, Technology Topic, Popular Technical Reports.
© 2024 PatSnap. All rights reserved.Legal|Privacy policy|Modern Slavery Act Transparency Statement|Sitemap|About US| Contact US: help@patsnap.com