Vertical type winding device for composite-material thin-wall high flange cylinder and manufacturing method
A high flanged cylinder and composite material technology, applied in the field of flanged cylinder manufacturing, can solve the problems of inability to apply pressure, the texture of the flange is loose, the longitudinal fibers of the cylinder section are turned over to a predetermined position, etc., and the effect of improving work efficiency is achieved.
- Summary
- Abstract
- Description
- Claims
- Application Information
AI Technical Summary
Problems solved by technology
Method used
Image
Examples
specific Embodiment approach 1
[0018] Specific implementation mode one: combine figure 1 with figure 2 To illustrate this embodiment, the vertical winding device used in this embodiment for thin-walled high-flange cylinders of composite materials includes a rotating shaft 1, a winding die 2 and two pressure plates 3;
[0019] The rotating shaft 1 is vertically arranged on the frame and can rotate. The winding die 2 is fixed on the rotating shaft 1. The winding die 2 is processed with a first cylinder 2-1 and a second cylinder 2-2. The first cylinder 2- The diameter of 1 is larger than the diameter of the second cylinder 2-2, the first cylinder 2-1 and the second cylinder 2-2 are respectively concentric with the rotating shaft 1, and the side of the first cylinder 2-1 is connected with a pressure plate by screws 3 connection, the side of the second cylinder 2-2 is connected with another pressure plate 3 by bolts.
[0020] The winding die 2 is processed with a first cylinder 2-1 and a second cylinder 2-2 t...
specific Embodiment approach 2
[0022] Specific implementation mode two: combination figure 1 To describe this embodiment, the height of the first cylinder 2-1 in this embodiment is greater than the height of the second cylinder 2-2.
[0023] Such arrangement is used to adapt to the cylinder body of the flange cylinder 4 to be wound.
[0024] Other compositions and connections are the same as in the first embodiment.
specific Embodiment approach 3
[0025] Specific implementation mode three: combination figure 1 To describe this embodiment, the two pressing plates 3 in this embodiment are both annular plates.
[0026] With such arrangement, the stress on the two flanges on the flange barrel 4 after flanging is uniform, so that the fiber arrangement of the flanging flange is uniform and accurate.
[0027] Its composition and connection relationship are the same as those in the second embodiment.
PUM
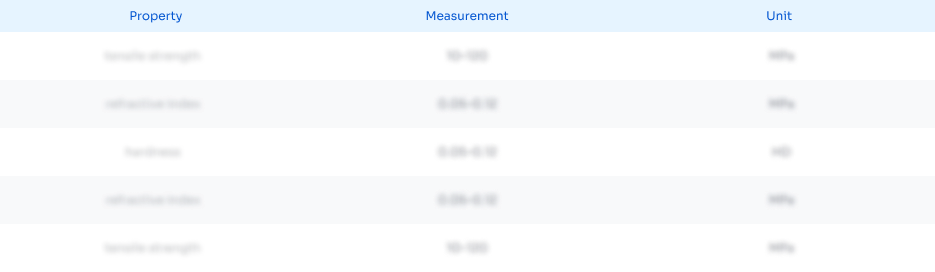
Abstract
Description
Claims
Application Information

- R&D
- Intellectual Property
- Life Sciences
- Materials
- Tech Scout
- Unparalleled Data Quality
- Higher Quality Content
- 60% Fewer Hallucinations
Browse by: Latest US Patents, China's latest patents, Technical Efficacy Thesaurus, Application Domain, Technology Topic, Popular Technical Reports.
© 2025 PatSnap. All rights reserved.Legal|Privacy policy|Modern Slavery Act Transparency Statement|Sitemap|About US| Contact US: help@patsnap.com