Improved yarn oiling machine
An improved yarn technology, which is applied in the field of textile yarn processing, can solve problems such as oil pollution, yarn quality, and easy adhesion, and achieve good versatility and strong versatility
- Summary
- Abstract
- Description
- Claims
- Application Information
AI Technical Summary
Problems solved by technology
Method used
Image
Examples
Embodiment Construction
[0029] Compared with the traditional dip-dyeing oiling device, the present invention improves on the above-mentioned three major defects in the background technology to solve the defects in the prior art, and makes the dip-dyeing oiling machine reach a higher technical height.
[0030] like Figure 1-9 An improved yarn oiling machine shown includes a dip-dyeing oiling device 1 and a spring-type oiling device 2 located on one side of the dipping-dyeing oiling device 1, and the dip-dyeing oiling device 1 The oiling device that carries out oiling to yarn 0 in the mode of the present invention, it has an oily liquid containing container that fills oily liquid 24. The spring-type degreasing device 2 is used to remove the excess oil 24 entrained on the yarn 0 after dipping. 2. Remove excess oil 24 by vibrating the yarn 0. Yarn 0 passes through the dip-dyeing oiling device 1 and the spring-type oiling device 2 sequentially along the conveying direction, that is to say, the yarn 0 p...
PUM
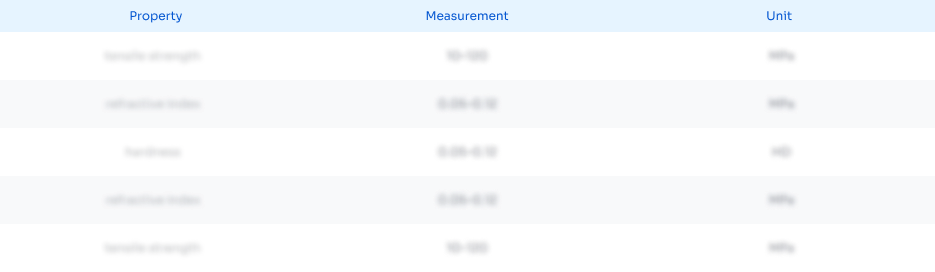
Abstract
Description
Claims
Application Information

- R&D
- Intellectual Property
- Life Sciences
- Materials
- Tech Scout
- Unparalleled Data Quality
- Higher Quality Content
- 60% Fewer Hallucinations
Browse by: Latest US Patents, China's latest patents, Technical Efficacy Thesaurus, Application Domain, Technology Topic, Popular Technical Reports.
© 2025 PatSnap. All rights reserved.Legal|Privacy policy|Modern Slavery Act Transparency Statement|Sitemap|About US| Contact US: help@patsnap.com