a plunger pump
A plunger pump and plunger technology, applied in pump components, pump control, variable capacity pump components, etc., can solve the problems of large floor space, large size of double-pump confluence unloading valve, and high cost
- Summary
- Abstract
- Description
- Claims
- Application Information
AI Technical Summary
Problems solved by technology
Method used
Image
Examples
Embodiment Construction
[0031] see Figure 1-11 As shown, a plunger pump includes a pump body 2, and a pump casing 1 installed on the right end surface of the pump body 2, and an oil inlet chamber 1a is formed between the pump casing 1 and the right end surface of the pump body 2. The left end surface of the pump body 2 is provided with an oil inlet hole 1b communicating with the oil inlet chamber 1a; the right end surface of the pump body 2 is rotatably connected with a rotating shaft 12 protruding from the pump casing 1, and the oil inlet chamber 1a is inside the pump body On the right end surface of 2, three variable plunger modules 001 are evenly installed with the rotating shaft 12 as the center, and the first shaft sleeves arranged side by side and coaxially are installed eccentrically on the rotating shaft 12 through the pin key 13a in the oil inlet chamber 1a 9b1 and the second sleeve 9b2.
[0032] The variable plunger module 001 includes a mounting block 3, a first plunger 7a, a second plun...
PUM
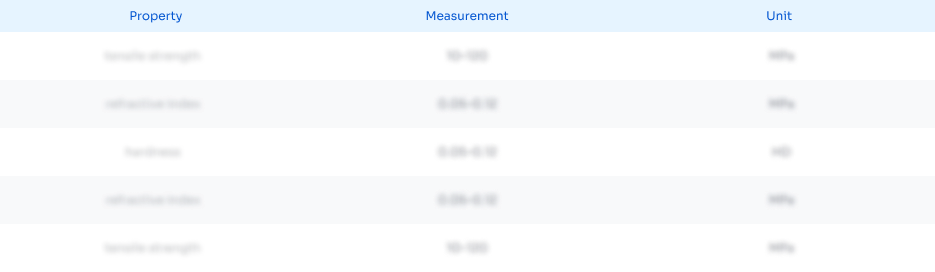
Abstract
Description
Claims
Application Information

- R&D Engineer
- R&D Manager
- IP Professional
- Industry Leading Data Capabilities
- Powerful AI technology
- Patent DNA Extraction
Browse by: Latest US Patents, China's latest patents, Technical Efficacy Thesaurus, Application Domain, Technology Topic, Popular Technical Reports.
© 2024 PatSnap. All rights reserved.Legal|Privacy policy|Modern Slavery Act Transparency Statement|Sitemap|About US| Contact US: help@patsnap.com