A kind of preparation method of polyester nylon composite elastic fiber
A composite technology of elastic fiber and polyester nylon, which is applied in the field of spinning to achieve good crimp elasticity and improved compatibility
- Summary
- Abstract
- Description
- Claims
- Application Information
AI Technical Summary
Problems solved by technology
Method used
Image
Examples
preparation example Construction
[0030] A preparation method of polyester nylon composite elastic fiber, comprising the following steps:
[0031] 1) Adding a third monomer with a total monomer amount of 1.5 to 2.5 mol / % to polyester monomers to synthesize modified polyester chips.
[0032] 2) Drying the modified polyester slices and nylon 6 slices respectively. The drying temperature of the modified polyester chips is 120-140° C., the drying time is 20 hours, and the water content of the resin after drying treatment is less than 30 ppm. The drying temperature of nylon 6 chips is 90-100°C, the drying time is 24 hours, and the water content of the resin after drying treatment is less than 100ppm.
[0033] Blend the dried modified polyester chips and nylon 6 chips, wherein the intrinsic viscosity of the modified polyester chips is 0.50-0.65dl / g, the relative viscosity of the nylon 6 chips is 2.47-2.52, the modified polyester chips and nylon The mass ratio of slices is 80:20-60:40.
[0034] Polyester and nylon...
Embodiment 1
[0041] A preparation method of polyester nylon composite elastic fiber, comprising the following steps:
[0042] 1) Add a third monomer of 2 mol / % total monomer amount to the polyester monomer, the third monomer is sodium ethylene glycol sulfonate isophthalate, and synthesize modified polyester chips.
[0043] 2) Drying the modified polyester slices and nylon 6 slices respectively. The drying temperature of the modified polyester chips is 130°C, the drying time is 20 hours, and the water content of the resin after drying treatment is less than 30ppm. The drying temperature of nylon 6 chips is 95°C, the drying time is 24 hours, and the water content of the resin after drying treatment is less than 100ppm.
[0044] The modified polyester chips and nylon 6 chips that have been dried are blended for 3 minutes, wherein the intrinsic viscosity of the modified polyester chips is 0.50dl / g, the relative viscosity of the nylon 6 chips is 2.48, and the quality of the modified polyester ...
Embodiment 2
[0051] A preparation method of polyester nylon composite elastic fiber, comprising the following steps:
[0052] 1) Add a third monomer with a total monomer amount of 2 mol / % to the polyester monomer, the third monomer is sodium ethylene glycol phthalate sulfonate, and synthesize modified polyester chips.
[0053] 2) Drying the modified polyester slices and nylon 6 slices respectively. The drying temperature of the modified polyester chips is 130°C, the drying time is 20 hours, and the water content of the resin after drying treatment is less than 30ppm. The drying temperature of nylon 6 chips is 100°C, and the drying time is 24 hours. After drying, the water content of the resin is less than 100ppm.
[0054] The modified polyester chips and nylon 6 chips that have been dried are blended for 3 minutes, wherein the intrinsic viscosity of the modified polyester chips is 0.52dl / g, the relative viscosity of the nylon 6 chips is 2.48, and the quality of the modified polyester chip...
PUM
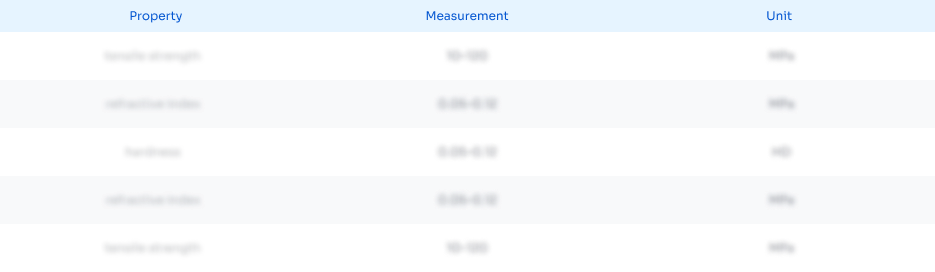
Abstract
Description
Claims
Application Information

- R&D
- Intellectual Property
- Life Sciences
- Materials
- Tech Scout
- Unparalleled Data Quality
- Higher Quality Content
- 60% Fewer Hallucinations
Browse by: Latest US Patents, China's latest patents, Technical Efficacy Thesaurus, Application Domain, Technology Topic, Popular Technical Reports.
© 2025 PatSnap. All rights reserved.Legal|Privacy policy|Modern Slavery Act Transparency Statement|Sitemap|About US| Contact US: help@patsnap.com