Preparation method of polyaspartate resin
An aspartic acid ester and resin technology, applied in the direction of polyurea/polyurethane coatings, coatings, etc., can solve the problems of expanding the scope of use, prolonging the construction time, and reducing the reaction speed of aliphatic isocyanates by polyaspartic acid resin. Achieve the effect of extending the operating time and expanding the scope of application
- Summary
- Abstract
- Description
- Claims
- Application Information
AI Technical Summary
Problems solved by technology
Method used
Examples
Embodiment 1
[0019] The raw materials were weighed according to the molar ratio of 4,4'-diaminodicyclohexylmethane, diethyl maleate and methyl acrylate as 1:2:0.05. First, add 4,4'-diaminodicyclohexylmethane into the reaction vessel, add diethyl maleate into the dropping device, control the temperature below 60°C for dropwise addition, and raise the temperature to 70-80°C after the dropwise addition °C for 150 hours; then lower the temperature to 40-50 °C, then add methyl acrylate dropwise at 40-50 °C for 24 hours. After the reaction, the film evaporated the unreacted diethyl maleate and methyl acrylate to obtain polyaspartic acid ester resin. After testing, the pot life of polyaspartic acid ester resin and HDI trimer curing agent is 26 minutes.
Embodiment 2
[0021] The raw materials were weighed according to the molar ratio of 4,4'-diaminodicyclohexylmethane, diethyl maleate and methyl acrylate as 1:2.2:0.05. First, add 4,4'-diaminodicyclohexylmethane into the reaction vessel, add diethyl maleate into the dropping device, control the temperature below 60°C for dropwise addition, and raise the temperature to 80-90°C after the dropwise addition °C for 110 hours; then lower the temperature to 50-60 °C, then add methyl acrylate dropwise at 50-60 °C for 20 hours. After the reaction, the film evaporated the unreacted diethyl maleate and methyl acrylate to obtain polyaspartic acid ester resin. After testing, the pot life of polyaspartic acid ester resin and HDI trimer curing agent is 27 minutes.
Embodiment 3
[0023] Weigh the raw materials according to the molar ratio of 4,4'-diaminodicyclohexylmethane, diethyl maleate and methyl acrylate as 1:2:0.1. First, add the diethyl maleate to the reaction vessel Add it into the dropping device, control the temperature below 60°C for dropwise addition, after the dropwise addition, raise the temperature to 70-80°C and react for 150 hours; then cool down to 40-50°C, then add dropwise methyl acrylate at 40-50°C for 24 hours Hour. After the reaction, the film evaporated the unreacted diethyl maleate and methyl acrylate to obtain polyaspartic acid ester resin. After testing, the pot life of polyaspartic acid ester resin and HDI trimer curing agent is 26 minutes.
PUM
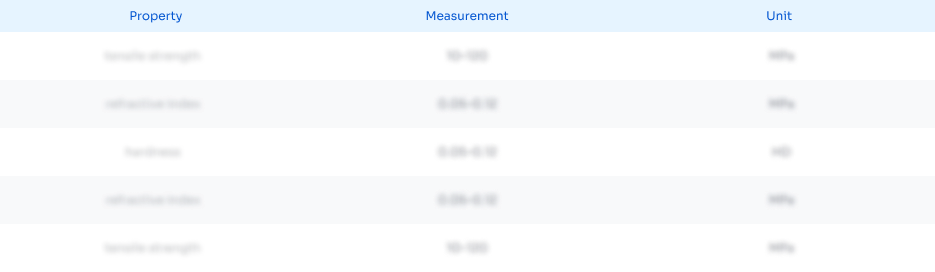
Abstract
Description
Claims
Application Information

- R&D
- Intellectual Property
- Life Sciences
- Materials
- Tech Scout
- Unparalleled Data Quality
- Higher Quality Content
- 60% Fewer Hallucinations
Browse by: Latest US Patents, China's latest patents, Technical Efficacy Thesaurus, Application Domain, Technology Topic, Popular Technical Reports.
© 2025 PatSnap. All rights reserved.Legal|Privacy policy|Modern Slavery Act Transparency Statement|Sitemap|About US| Contact US: help@patsnap.com