Flax fiber yarn automatic production line and production process thereof
An automatic production line, flax technology, applied in textile and papermaking, mechanical processing, fiber processing, etc., can solve problems such as low efficiency, affecting flax drawing, coarse sand, and affecting the quality of finished products
- Summary
- Abstract
- Description
- Claims
- Application Information
AI Technical Summary
Problems solved by technology
Method used
Image
Examples
Embodiment 1
[0066] Such as Figures 1 to 15 As shown, an automatic linen yarn production line includes a track 1 and a clamping mechanism 2 that clamps the flax and drives it to make a rotary motion along the track 1. There is a feeding part 3, a first comb part 4, a turning part 5, a second comb part 6 and a retrieving part 7; the clamping mechanism 2 includes an upper clamping assembly 21 and a lower clamping assembly 22;
[0067] The feeding part 3 includes a guiding and separating mechanism 31 arranged above the track 1, a dialing mechanism 32 arranged inside the track 1, a transmission mechanism 33 arranged on the outside of the track 1, and a guide and separating mechanism 31 at the tail end of the guiding and separating mechanism. A tightening mechanism 34 and a transfer mechanism 35 arranged on one side of the transmission mechanism 33;
[0068] The dialing mechanism 32 is used to dial the clamping mechanism 2 that has completed the material fetching at the fetching part 7 to the...
Embodiment 2
[0090] Such as Figure 5 and Figure 6 As shown, the components that are the same as or corresponding to those in the first embodiment are marked with the corresponding reference numerals in the first embodiment. For the sake of simplicity, only the differences from the first embodiment will be described below. The difference between the second embodiment and the first embodiment is that further, the push assembly 351 includes a fixed seat 3511, a flat pusher 3512 arranged on the fixed seat 3511, and a push plate 3513 driven by the flat pusher 3512 , the upper surface of the push plate 3513 is rotatably provided with several guide rollers 3514;
[0091] The adapter assembly 352 includes an adapter plate 3521 fixed on the rail 1, the adapter plate 3521 is below the push plate 3513, and the rear end of the adapter plate 3521 is rotatably provided with a dial roller 3522, the One end of the dial roller 3522 is provided with a third gear 3523 which is coaxial with the dial rolle...
Embodiment 3
[0094] Such as Figure 16 As shown, the present invention also provides a flax automatic production process, including the following production steps: combing part, pretreatment part, drawing part, roving part, boiling and bleaching part, spun yarn part, winding part and finished product packaging part; Wherein, the comb part described in the present invention specifically includes the following steps:
[0095] a. separation process, the clamping mechanism 2 is transported along the track 1, and the upper clamping assembly 21 and the lower clamping assembly 22 are separated up and down under the action of the guiding separation mechanism 31;
[0096] b. The feeding process, the upper and lower clamping components 21 and the lower clamping components 22 that have been separated up and down in the step a are synchronously transported to the feeding station under the action of the dialing mechanism 32, and at the same time, the transmission mechanism 33 will The flax is transfer...
PUM
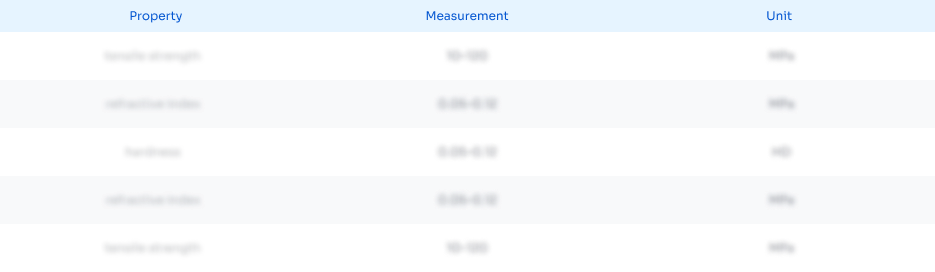
Abstract
Description
Claims
Application Information

- R&D Engineer
- R&D Manager
- IP Professional
- Industry Leading Data Capabilities
- Powerful AI technology
- Patent DNA Extraction
Browse by: Latest US Patents, China's latest patents, Technical Efficacy Thesaurus, Application Domain, Technology Topic, Popular Technical Reports.
© 2024 PatSnap. All rights reserved.Legal|Privacy policy|Modern Slavery Act Transparency Statement|Sitemap|About US| Contact US: help@patsnap.com