Roller material of filling machine and preparation method thereof
A filling machine and drum technology, which is applied in the field of filling machine drum material and its preparation, can solve the problems of low drum strength and short service life, achieve quality assurance, reduce instability, and improve mechanical properties and thermal stability. Effect
- Summary
- Abstract
- Description
- Claims
- Application Information
AI Technical Summary
Problems solved by technology
Method used
Examples
Embodiment 1
[0018] A method for preparing a drum material for a filling machine, comprising the following steps:
[0019] (1) Weigh the following raw materials in weight percentage respectively: 0.03% of carbon fiber, 0.035% of epoxy resin, 5% of zinc oxide, 0.25% of maleic anhydride grafted polypropylene, 0.015% of nano titanium dioxide, 9.50% of n-propyl methacrylate , tripropylene glycol diacrylate 0.25%, nano calcium sulfate 0.15%, zirconia 0.50%, polyethylene terephthalate 0.15%, bronze powder 0.15%, graphite 0.04%, tungsten carbide 0.01%, silica lime 0.050 %, polyethylene glass fiber 0.018% and calcium stearate 0.01%, the balance is mica active calcium;
[0020] (2) Carbon fiber, epoxy resin, zinc oxide, maleic anhydride grafted polypropylene, nano-titanium dioxide, n-propyl methacrylate, tripropylene glycol diacrylate, nano-calcium sulfate, oxide Zirconium, mica active calcium, polyethylene terephthalate, bronze powder, graphite and tungsten carbide are sequentially added to the e...
Embodiment 2
[0027] A method for preparing a drum material for a filling machine, comprising the following steps:
[0028] (1) Weigh the following raw materials in weight percentage respectively: 0.04% of carbon fiber, 0.04% of epoxy resin, 5.5% of zinc oxide, 0.3% of P element, 0.016% of nano titanium dioxide, 10% of n-propyl methacrylate, tripropylene glycol Acrylic ester 0.30%, nano calcium sulfate 0.17%, zirconia 0.55%, polyethylene terephthalate 0.16%, bronze powder 0.155%, graphite 0.045%, tungsten carbide 0.012%, silica lime 0.040%, polyethylene glass 0.019% fiber and 0.012% calcium stearate, the balance is active calcium mica;
[0029] (2) Carbon fiber, epoxy resin, zinc oxide, maleic anhydride grafted polypropylene, nano-titanium dioxide, n-propyl methacrylate, tripropylene glycol diacrylate, nano-calcium sulfate, oxide Zirconium, mica active calcium, polyethylene terephthalate, bronze powder, graphite and tungsten carbide are sequentially added to the electric melting furnace fo...
Embodiment 3
[0036] A method for preparing a drum material for a filling machine, comprising the following steps:
[0037] (1) Weigh the raw materials in the following percentages by weight: carbon fiber 0.05%, epoxy resin 0.05%, zinc oxide 6%, maleic anhydride grafted polypropylene 0.35%, nano-titanium dioxide 0.017%, n-propyl methacrylate 10.5% , tripropylene glycol diacrylate 0.50%, nano calcium sulfate 0.20%, zirconia 0.60%, polyethylene terephthalate 0.17%, bronze powder 0.16%, graphite 0.05%, tungsten carbide 0.015%, silica lime 0.060 %, polyethylene glass fiber 0.020% and calcium stearate 0.015%, the balance is mica active calcium;
[0038] (2) Carbon fiber, epoxy resin, zinc oxide, maleic anhydride grafted polypropylene, nano-titanium dioxide, n-propyl methacrylate, tripropylene glycol diacrylate, nano-calcium sulfate, oxide Zirconium, mica active calcium, polyethylene terephthalate, bronze powder, graphite and tungsten carbide are sequentially added to the electric melting furnac...
PUM
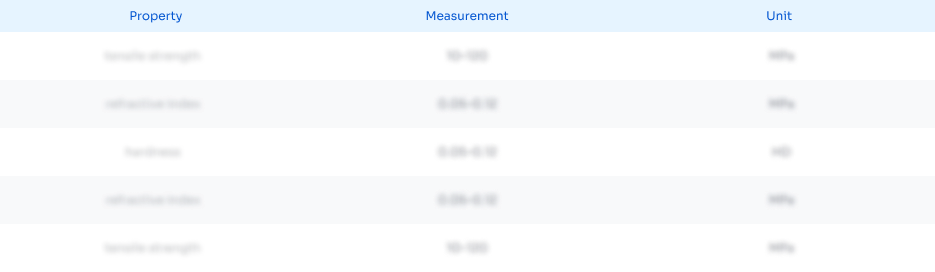
Abstract
Description
Claims
Application Information

- Generate Ideas
- Intellectual Property
- Life Sciences
- Materials
- Tech Scout
- Unparalleled Data Quality
- Higher Quality Content
- 60% Fewer Hallucinations
Browse by: Latest US Patents, China's latest patents, Technical Efficacy Thesaurus, Application Domain, Technology Topic, Popular Technical Reports.
© 2025 PatSnap. All rights reserved.Legal|Privacy policy|Modern Slavery Act Transparency Statement|Sitemap|About US| Contact US: help@patsnap.com