Red matt glaze
A matte glaze and red technology, which is applied in the field of Jun porcelain red matte glaze and its preparation, can solve the problems of high cost, rough glaze surface, poor color glaze adaptability, etc., and achieve high yield and smooth and delicate glaze surface Effect
- Summary
- Abstract
- Description
- Claims
- Application Information
AI Technical Summary
Problems solved by technology
Method used
Image
Examples
Embodiment 1
[0018] A red matt glaze, which is composed of the following raw materials in parts by weight: feldspar 32-38, quartz 11-13, calcite 9-11, talc 11-13, wollastonite 7-9, copper ore 10-14, Kaolin 6-8, zinc oxide 1.5-2.5, aluminum oxide 1.5-2.5.
[0019] The preparation method of the above-mentioned red matte glaze comprises the following steps:
[0020] (1) Mix the raw materials; ball mill to obtain the glaze slurry; pass the glaze slurry through a sieve of more than 200 mesh;
[0021] (2) Glaze is applied to the carcass after bisque firing; the thickness of the glaze is 0.6-0.8mm;
[0022] (3) Firing: First, the temperature of the glazed carcass is raised to 1000-1100°C evenly in 3.5-4.5h in an oxidizing atmosphere; then the temperature is evenly raised to 1300-1320°C in 2-3h in a reducing atmosphere ; Keep warm for 25-60 minutes, then keep warm and cool, and cool to room temperature for more than 6 hours.
[0023] The feldspar, quartz, calcite, talc, wollastonite, copper ore...
Embodiment 2
[0026] A red matte glaze is composed of the following raw materials in parts by weight: 35 feldspar, 12 quartz, 10 calcite, 12 talc, 8 wollastonite, 12 copper ore, 7 kaolin, 2 zinc oxide and 2 aluminum oxide.
[0027] The preparation method of the above-mentioned red matte glaze comprises the following steps:
[0028] (1) Mix the raw materials; ball mill to obtain the glaze slurry; pass the glaze slurry through a sieve of more than 200 mesh;
[0029] (2) Glaze is applied to the carcass after bisque firing; the thickness of the glaze is 0.6-0.8mm;
[0030] (3) Firing: first, the temperature of the glazed carcass is uniformly raised to 1050°C in 4 hours in an oxidizing atmosphere; then in a reducing atmosphere, the temperature is evenly raised to 1310°C in 2.5 hours; kept for 40 minutes, and then cooled in 7 hours to room temperature.
[0031] The glaze prepared in this example is smooth and fine, with a glossiness of 4.1%. The finished product rate can reach 92% by gas burni...
PUM
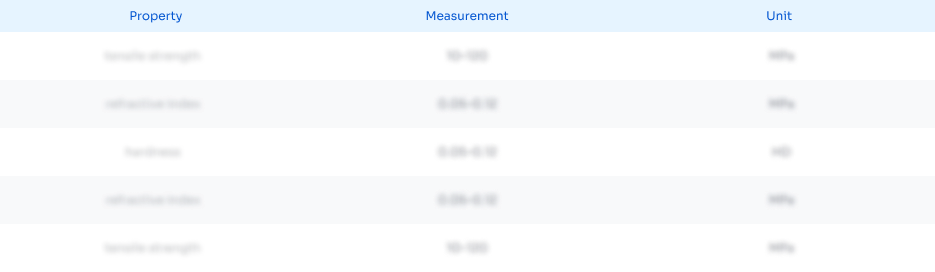
Abstract
Description
Claims
Application Information

- R&D Engineer
- R&D Manager
- IP Professional
- Industry Leading Data Capabilities
- Powerful AI technology
- Patent DNA Extraction
Browse by: Latest US Patents, China's latest patents, Technical Efficacy Thesaurus, Application Domain, Technology Topic, Popular Technical Reports.
© 2024 PatSnap. All rights reserved.Legal|Privacy policy|Modern Slavery Act Transparency Statement|Sitemap|About US| Contact US: help@patsnap.com