High-performance continuous forging and pressing device for alloy steel rods
An alloy steel bar, high-performance technology, applied in forging/pressing/hammer devices, operating devices, metal processing equipment, etc., can solve the problems of discontinuous forging process, low work efficiency, manual refueling, etc.
- Summary
- Abstract
- Description
- Claims
- Application Information
AI Technical Summary
Problems solved by technology
Method used
Image
Examples
Embodiment Construction
[0016] The following will clearly and completely describe the technical solutions in the embodiments of the present invention with reference to the accompanying drawings in the embodiments of the present invention. Obviously, the described embodiments are only some of the embodiments of the present invention, not all of them. Based on the embodiments of the present invention, all other embodiments obtained by persons of ordinary skill in the art without making creative efforts belong to the protection scope of the present invention.
[0017] see Figure 1-4 , the present invention provides a technical solution: a high-performance alloy steel rod continuous forging device, including a workbench 1, a chute 2 is opened on the workbench 1, one end of the chute 2 is fixedly connected to a feed chute 9 on both sides, and the The steel bar 10 is slidably placed in the chute 9, the other end of the chute 2 is fixedly connected to the discharge chute 12, the workbench 1 on both sides o...
PUM
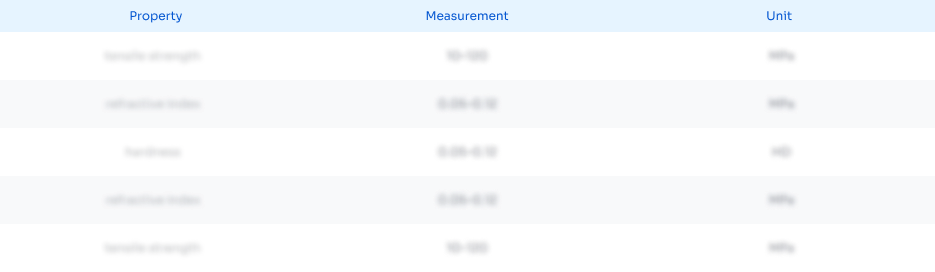
Abstract
Description
Claims
Application Information

- Generate Ideas
- Intellectual Property
- Life Sciences
- Materials
- Tech Scout
- Unparalleled Data Quality
- Higher Quality Content
- 60% Fewer Hallucinations
Browse by: Latest US Patents, China's latest patents, Technical Efficacy Thesaurus, Application Domain, Technology Topic, Popular Technical Reports.
© 2025 PatSnap. All rights reserved.Legal|Privacy policy|Modern Slavery Act Transparency Statement|Sitemap|About US| Contact US: help@patsnap.com