Bus capacitor discharge method, system and device for power device
A technology of power devices and bus capacitors, applied in the direction of output power conversion devices, control systems, motors, etc., can solve problems such as hazards
- Summary
- Abstract
- Description
- Claims
- Application Information
AI Technical Summary
Problems solved by technology
Method used
Image
Examples
Embodiment approach 1
[0205] In this embodiment, the power device includes a first active short-circuit control module. Specifically, see the attached Figure 4 , Figure 4 The control mode of the half-bridge circuit in this embodiment is shown as an example. In this embodiment, the DC bus capacitor can be discharged according to the following steps:
[0206] Step 1: Determine whether the active discharge start command is obtained: if yes, go to step 2; if not, continue to obtain the active discharge start command.
[0207] Step 2: Use the driver module of the lower bridge arm ( Figure 4 The driving module connected to IGBT2) controls the power semiconductor device IGBT2 in the lower bridge arm to turn on.
[0208] When the active circuit protection of the motor is required during the discharge process, according to the short circuit control signal ( Figure 4 The shown pulse signal ASC_CMD) triggers to start the first active short-circuit control module corresponding to IGBT2, and the first ...
Embodiment approach 2
[0213] In this embodiment, the power device includes a second active short-circuit control module. Specifically, see the attached Figure 5 , Figure 5 The control mode of the half-bridge circuit in this embodiment is shown as an example. In this embodiment, the DC bus capacitor can be discharged according to the following steps:
[0214] Step 1: Determine whether the active discharge start command is obtained: if yes, go to step 2; if not, continue to obtain the active discharge start command.
[0215] Step 2: Control the second active short-circuit control module ( Figure 5 The second active short-circuit control module connected to the shown IGBT2) according to the short-circuit control signal ( Figure 5 The shown pulse signal ASC_CMD) controls the power semiconductor device IGBT2 in the lower bridge arm to turn on.
[0216] Step 3: Switch the gate drive resistor of the power semiconductor device IGBT1 in the upper bridge arm to a resistor Rgon_large with a larger re...
PUM
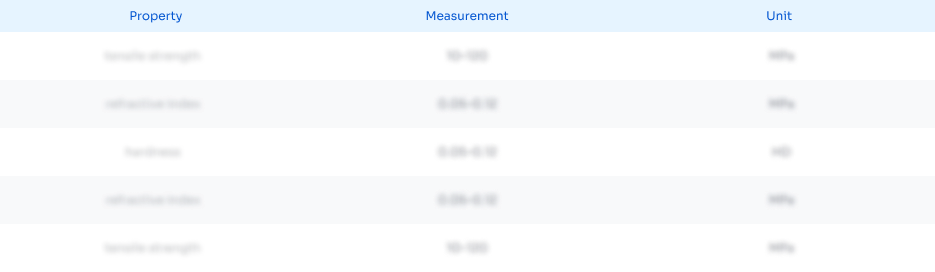
Abstract
Description
Claims
Application Information

- Generate Ideas
- Intellectual Property
- Life Sciences
- Materials
- Tech Scout
- Unparalleled Data Quality
- Higher Quality Content
- 60% Fewer Hallucinations
Browse by: Latest US Patents, China's latest patents, Technical Efficacy Thesaurus, Application Domain, Technology Topic, Popular Technical Reports.
© 2025 PatSnap. All rights reserved.Legal|Privacy policy|Modern Slavery Act Transparency Statement|Sitemap|About US| Contact US: help@patsnap.com