Dynamic and cyclic direct shear test method for rock mass structural planes
A test method and dynamic cycle technology are applied in the direction of testing material strength by applying stable shear force, testing material strength by applying repetitive force/pulsation force, and measuring devices, which can solve the lack of understanding of dynamic cycle shear characteristics, Lack of other issues
- Summary
- Abstract
- Description
- Claims
- Application Information
AI Technical Summary
Problems solved by technology
Method used
Image
Examples
Embodiment 1
[0036] Please refer to figure 1 and figure 2 , The steps of the uniform velocity unidirectional direct shear test method for the rock mass structure surface are: first, the normal load is applied to the rock mass structure surface 3 by controlling the normal oil cylinder 1 and the upper shear box 2; The lower shear box 5 is pushed out to the oil cylinder 4 at a constant speed and then acts on the rock mass structure surface 3. The rock mass structure surface 3 is the contact between the upper shear box 2 and the rock blocks in the lower shear box 5. The length of the rock blocks in the upper shear box 2 along the shear direction is smaller than that in the lower shear box 5, and the moving speed of the lower shear box 5 is determined according to the dynamic test requirements, and the rate range can be selected from 0.001 to 1000mm / s; during the test, the test data is recorded by the force sensor 6 and the displacement sensor 7; finally, the test is stopped when the lower sh...
Embodiment 2
[0038] Please refer to figure 1 and image 3 , The steps of the variable-speed unidirectional direct shear test method for the rock mass structure surface are: first, the normal load is applied to the rock mass structure surface 3 by controlling the normal oil cylinder 1 and the upper shear box 2; The lower shear box 5 is pushed out to the oil cylinder 4 at a constant shear direction and at a changing rate, and then acts on the rock mass structure surface 3. The movement rate of the lower shear box 5 is determined according to the dynamic test requirements; during the test, the force The sensor 6 and the displacement sensor 7 record the test data; finally, the test is stopped when the lower shear box 5 moves to the preset position, and the distance between the preset position and the displacement zero point is between 0 and the rock blocks in the lower and upper shear boxes. Between the length differences and the rock blocks in the upper shear box are never separated from the...
Embodiment 3
[0040] Please refer to Figure 4 and Figure 5, The steps of the one-way cyclic direct shear test method for the rock mass structure surface are: first, the normal load is applied to the rock mass structure surface 3 through the control normal oil cylinder 1 and the upper shear box 2; The lower shear box 5 is pushed out to the oil cylinder 4 at a constant shearing direction and a certain speed, and then acts on the rock mass structure surface 3. When the lower shear box 5 moves to the preset position, the tangential oil cylinder 4 is pushed out by controlling the tangential oil cylinder 4. Then pull back the lower shear box 5, the distance between the preset position and the displacement zero point is between the 0 value and the difference between the lengths of the rock blocks in the lower and upper shear boxes, and the rock blocks in the upper shear box are always Do not detach from the rock block surface in the lower shear box; when the lower shear box 5 moves to the displ...
PUM
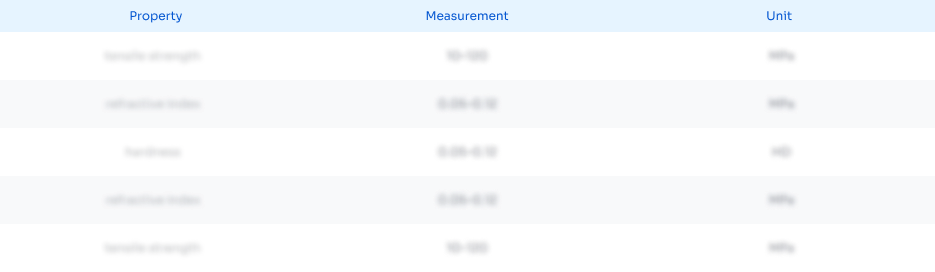
Abstract
Description
Claims
Application Information

- R&D
- Intellectual Property
- Life Sciences
- Materials
- Tech Scout
- Unparalleled Data Quality
- Higher Quality Content
- 60% Fewer Hallucinations
Browse by: Latest US Patents, China's latest patents, Technical Efficacy Thesaurus, Application Domain, Technology Topic, Popular Technical Reports.
© 2025 PatSnap. All rights reserved.Legal|Privacy policy|Modern Slavery Act Transparency Statement|Sitemap|About US| Contact US: help@patsnap.com